1. Invoering
In de sieradenbranche, the aesthetic appeal and quality of engraved pieces can set a brand apart. With a growing trend towards personalization and custom design, UV laser engraving has become a popular method due to its precision and versatility. Echter, one of the most critical decisions is selecting the appropriate laser power. This article explores whether a 5W or a 10W UV laser is better suited for jewelry engraving, taking into account both performance and cost.
2. Understanding UV Laser Power
2.1 How UV Lasers Work
UV lasers operate by emitting ultraviolet light at a specific wavelength—typically around 355nm. This wavelength is ideal for delicate materials, as it allows for high-resolution engraving with minimal thermal damage. In jewelry engraving, this means you can achieve crisp, detailed designs on materials like metals, edelstenen, and even certain plastics without compromising their integrity.
2.2 Key Differences Between 5W and 10W Lasers
The power rating of a UV laser—measured in watts—significantly impacts its performance:
- 5W UV Lasers:
- Lower Power Consumption: Ideal for small-scale operations and delicate work.
- Fine Detail: Generally provides excellent resolution and precision, suitable for intricate designs.
- Kosteneffectief: Lower upfront cost and operational expenses, making them attractive for startups and hobbyists.
- 10W UV Lasers:
- Higher Power Output: Capable of engraving deeper and at faster speeds, which can be beneficial for high-volume production.
- Enhanced Versatility: Better suited for a wider range of materials, including slightly thicker or harder substrates.
- Increased Efficiency: Potential for shorter processing times, leading to higher throughput in production settings.
Understanding these differences is crucial for UV laser power selection, especially when balancing quality and jewelry engraving cost.
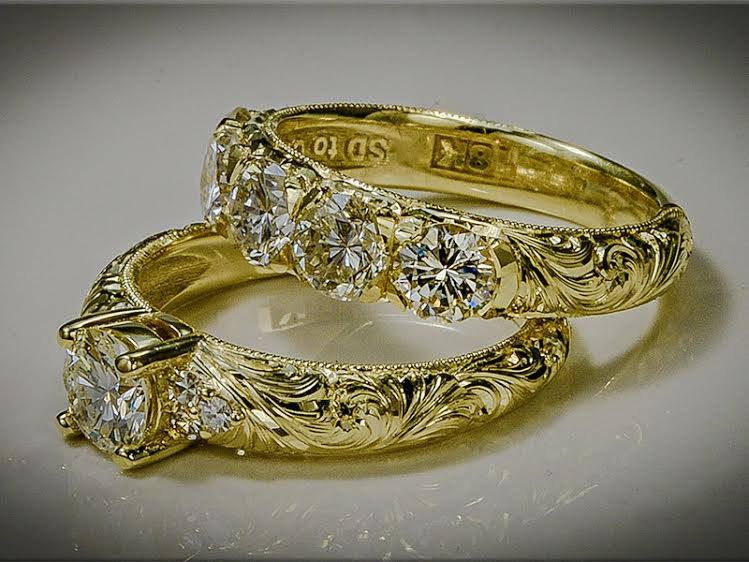
3. Engraving Jewelry: Specific Needs and Challenges
3.1 Material Considerations
Jewelry engraving typically involves working with materials such as:
- Precious Metals: Goud, zilver, and platinum require precise control to avoid excessive heat, which could distort the metal.
- Niet-metalen: Materials like leather, acryl, and even gemstones are sensitive to laser power and require gentle handling.
- Composite Materials: Soms, jewelry pieces may incorporate a mix of metals and non-metals, necessitating a versatile laser solution.
3.2 Detail and Precision Requirements
For jewelry, the engraving must capture intricate details—down to the micron level—to ensure that designs such as logos, patronen, or personalized inscriptions are crisp and elegant. This level of detail often means that even slight deviations in calibration or laser power can lead to suboptimal results. Daarom, achieving 0.001mm precision is often the benchmark for high-quality jewelry engraving.
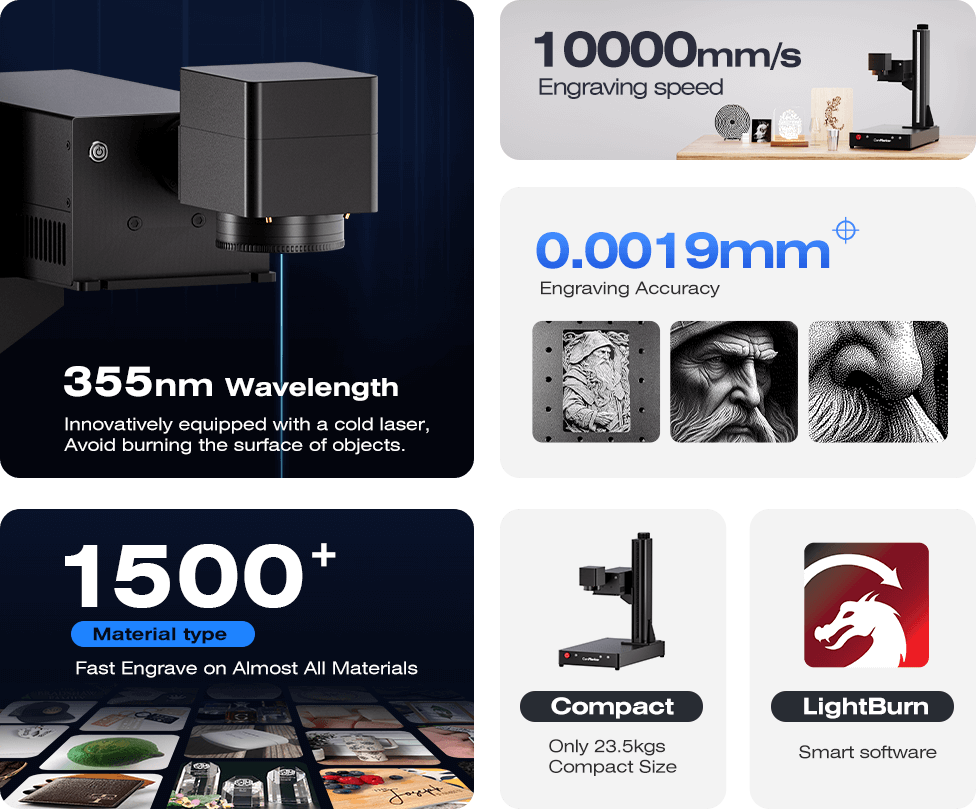
4. 5W UV Lasers for Jewelry Engraving
4.1 Voordelen
- High Resolution and Detail:
A 5W UV laser is typically sufficient for detailed, fijne gravure. Its lower power output minimizes thermal effects, reducing the risk of melting or distorting delicate jewelry surfaces. - Energie-efficiëntie:
Lower wattage results in reduced power consumption, which can be an important consideration for small businesses and hobbyists. - Cost Savings:
With a lower purchase price and reduced operating costs, 5W UV lasers are ideal for startups or artisans who are just entering the market. - Ideal for Intricate Designs:
For applications that require extreme detail—such as engraving micro text, ingewikkelde patronen, or fine lines—a 5W laser often provides the necessary control and precision.
4.2 Beperkingen
- Limited Depth and Speed:
While excellent for fine details, a 5W UV laser may struggle with deeper engraving or higher throughput production compared to a 10W unit. - Materiële veelzijdigheid:
If your work involves engraving on a wider variety of materials or thicker substrates, the lower power may limit performance, necessitating longer processing times.
4.3 Cost Implications
For many jewelry artisans, cost is a significant factor. 5W UV lasers generally come with a lower upfront cost, and their energy efficiency translates into lower operating expenses. Aanvullend, the reduced power may also result in less wear and tear, potentially lowering maintenance costs over time. For businesses focused on small, intricate pieces, the cost savings can be substantial, making this option very attractive.
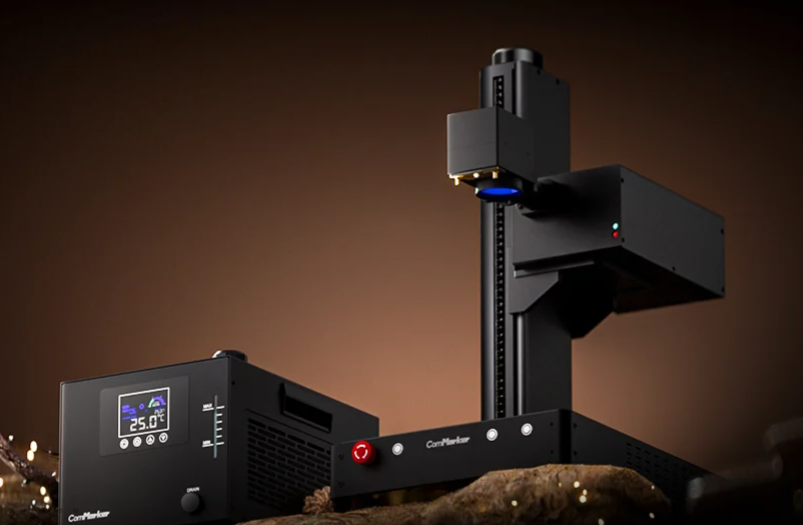
5. 10W UV Lasers for Jewelry Engraving
5.1 Voordelen
- Higher Power and Speed:
A 10W UV laser delivers more power, enabling faster engraving and the ability to achieve deeper markings. This is particularly beneficial for larger production runs or when working with materials that require higher energy for proper engraving. - Enhanced Material Flexibility:
The increased power output makes 10W lasers more versatile, allowing them to handle a broader range of materials, including slightly tougher or thicker substrates. - Improved Throughput:
In a production environment where time is money, the faster processing speeds of 10W lasers can significantly boost productivity.
5.2 Beperkingen
- Increased Thermal Impact:
With higher power comes a greater risk of thermal damage. Careful calibration and parameter adjustment are required to avoid overheating, especially on delicate materials like precious metals or thin gemstones. - Higher Operating Costs:
The increased power consumption may lead to higher electricity bills and potentially greater wear on the equipment, increasing maintenance costs. - Potential Overkill for Fine Details:
For ultra-fine, ingewikkelde ontwerpen, the excess power of a 10W laser might need to be carefully managed to avoid compromising detail and precision.
5.3 Cost Implications
Although 10W UV lasers are more expensive upfront and might incur higher operating costs, they can offer significant benefits in speed and versatility. For jewelry manufacturers with high production volumes or those that work with a diverse range of materials, the enhanced capabilities may justify the additional investment. The improved throughput can also lower the per-piece cost in a high-volume setting, balancing out the higher initial expense.
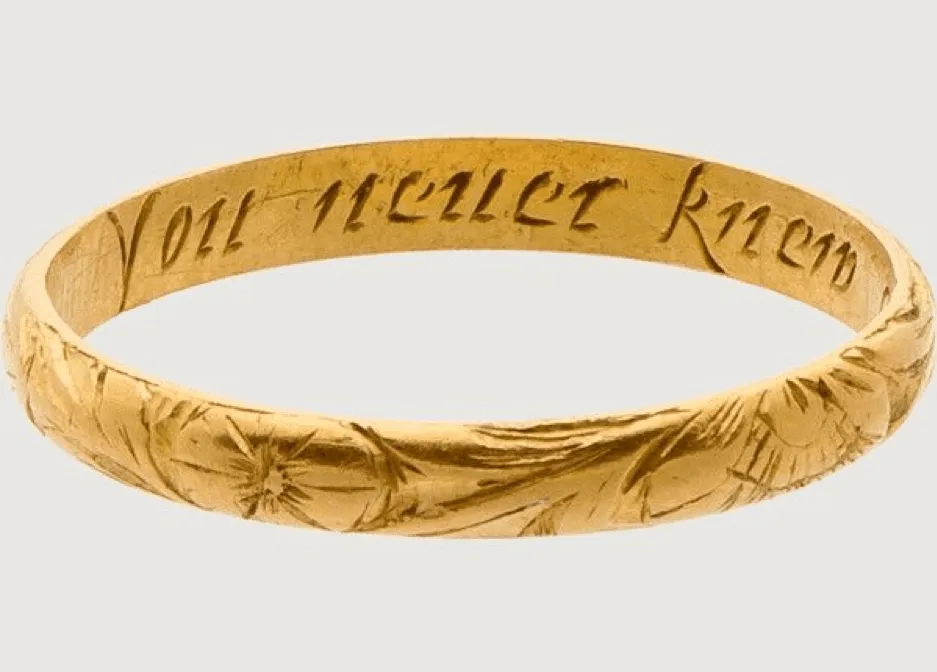
6. Comparison: 5W vs. 10W for Jewelry Engraving
Below is a comparison table that outlines the key differences:
Functie | 5W UV-laser | 10W UV-laser |
---|---|---|
Vermogen | Lager vermogen; ideal for delicate, detailed work | Hogere kracht; better for deeper engraving and faster production |
Gravureprecisie | High precision with minimal thermal impact | High precision, but requires careful parameter control to avoid overheating |
Snelheid | Sufficient for small-scale production | Faster processing; ideal for high-volume manufacturing |
Materiële veelzijdigheid | Best for delicate materials and fine details | Greater versatility; can handle tougher or thicker materials |
Kosten | Lower initial and operating cost | Higher upfront and operating cost, balanced by improved throughput |
Best Use Cases | Custom jewelry, fine art, low-volume production | Industrial-scale production, diverse material processing, high-volume operations |
This UV laser comparison clearly illustrates that the best choice depends on your specific requirements. For artisanal or boutique jewelry, where intricate detail is paramount, a 5W UV laser might be sufficient. For larger operations that demand speed, diepere gravure, and versatility across materials, a 10W UV laser is likely the better option.
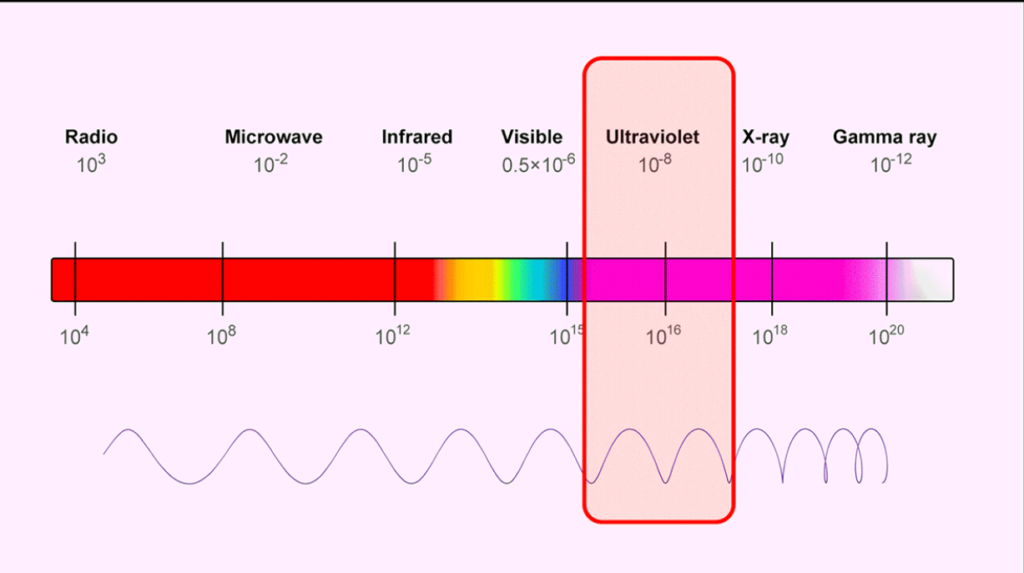
7. Making the Right UV Laser Power Selection
7.1 Beoordeel uw productiebehoeften
Before making a decision, overwegen:
- Volume: Are you producing a few custom pieces or thousands of items daily?
- Detail: How intricate are your designs? Do you require ultra-fine details or can you work with slightly less precision?
- Materiaal: What materials are you primarily engraving? Delicate substrates like glass and thin metals may benefit from lower power to avoid thermal damage.
- Begroting: Weigh the cost savings of a lower-powered unit against the potential need for faster throughput and deeper engraving in a high-volume setting.
7.2 Balancing Quality and Cost
While the 5W UV laser offers excellent precision and lower cost, the 10W UV laser’s speed and versatility can be a game-changer for production-scale operations. Evaluate your current and future needs to ensure your investment aligns with your business goals.
7.3 Expert Recommendations
- For Hobbyists and Small Businesses:
A 5W UV laser is often the best choice due to its lower cost, gebruiksgemak, and sufficient precision for custom jewelry and small-scale production. - For High-Volume Industrial Applications:
A 10W UV laser is recommended if you require faster processing speeds, the ability to engrave deeper, and versatility across various materials—even if it comes with a higher price tag.
ComMarker Omni 1 Lasergraveerder
Laser van de volgende generatie om alle materialen te ontgrendelen. ZeroBurn™-graveertechnologie 's werelds eerste 16K HD-lasergraveerder 10.000 mm/s SpeedMax™-graveersysteem Ontgrendel al het materiaal met UV-laser ColdFront™ thermische technologie Elektrisch heffen met 2 Optionele lenzen compatibel met EZCAD en LightBurn 360° roterend graveersysteem
8. Conclusie
Choosing the right UV laser for jewelry engraving ultimately depends on your specific production needs, the level of detail required, en uw budget. Here’s a quick recap:
- 5W UV Lasers:
- Pluspunten: High precision, minimale thermische impact, kosteneffectief, ideal for intricate, delicate work.
- Nadelen: Lower power may limit production speed and depth for high-volume operations.
- 10W UV Lasers:
- Pluspunten: Higher power for deeper engraving, faster processing, versatile across more materials.
- Nadelen: Increased thermal risk and higher operating costs require careful calibration.
For businesses seeking micron-level accuracy and exceptional detail, the 5W UV laser is a superb choice. Echter, if your operations demand higher throughput and the ability to handle a broader range of materials, the 10W UV laser may offer the performance edge needed to scale your production effectively.
Uiteindelijk, the decision should be based on a careful assessment of your production volume, materiaalcompatibiliteit, and cost considerations. Whichever you choose, proper calibration and maintenance will be key to maximizing your investment and achieving consistent, resultaten van hoge kwaliteit.