Material carbonization during laser engraving is a common challenge that can compromise the quality of your work. Whether you’re marking wood, akryl, lær, eller annet materiale, improper laser settings can lead to unwanted burns and carbon buildup, resulting in dark, uneven, or degraded finishes. I denne veiledningen, we provide actionable insights and detailed laser power and frequency settings for over 10 materialer. Our goal is to help you prevent engraving burns and material carbonization while maintaining optimal quality and precision in your projects.
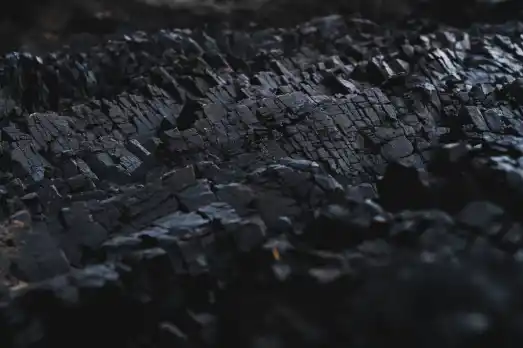
1. Understanding Material Carbonization
1.1 What is Material Carbonization?
Material carbonization is the process by which a material’s surface burns and converts into carbon. In laser engraving, this often manifests as a dark, uneven area where the laser has applied too much energy, leading to burning rather than clean cutting or marking. This undesirable outcome can detract from the aesthetics of the final product and affect its durability.
1.2 Common Causes in Laser Engraving
- Excessive Laser Power: When the laser output is too high, the energy can burn the material instead of precisely engraving it.
- Improper Frequency Settings: Low frequency settings may concentrate energy into a small area, causing overheating.
- Insufficient Cooling: Poor ventilation or inadequate cooling systems can lead to a buildup of heat.
- Material Sensitivity: Some materials are more prone to carbonization, requiring delicate handling and optimized settings.
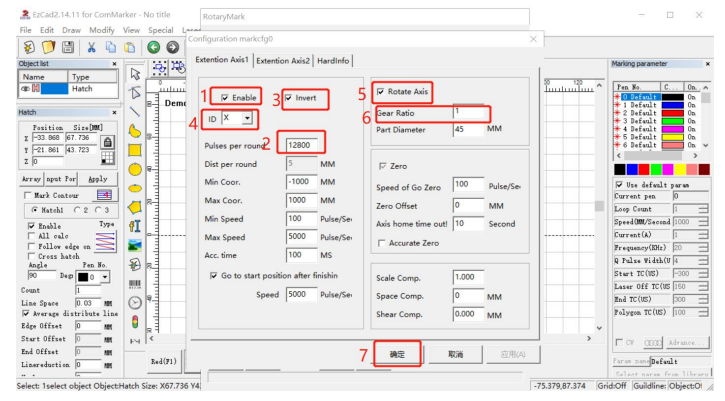
2. Fundamentals of Laser Power and Frequency Settings
2.1 Laserkraft: How It Affects Engraving
Laserkraft, typically measured in watts, determines the amount of energy delivered to the material. Finding the right balance is key:
- Lower Power: Minimizes heat accumulation, ideal for delicate materials.
- Higher Power: Enables faster engraving and deeper cuts but increases the risk of carbonization if not managed carefully.
2.2 Frequency Settings and Their Role
Frekvens, measured in kilohertz (kHz), influences how often the laser pulses per second:
- High Frequency: Provides a more continuous beam, leading to smoother engraving but can overheat sensitive materials if not controlled.
- Low Frequency: Reduces the overall energy input, which is beneficial for preventing carbonization but may result in slower processing speeds.
Balancing power and frequency is crucial to achieve clean, precise engravings without unwanted burns.
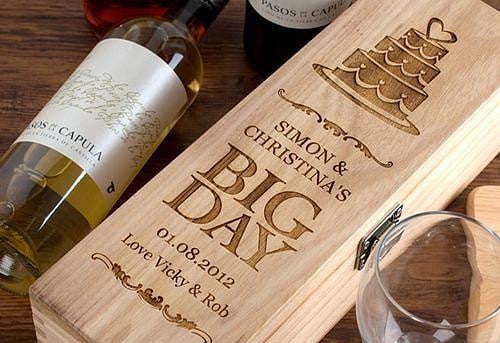
3. Preventing Engraving Burns: Best Practices
3.1 Pre-Engraving Preparation
Proper preparation is essential to prevent material carbonization:
- Material Inspection: Ensure that the material is clean, free of contaminants, and properly secured.
- Cooling System Check: Verify that your laser engraver’s cooling system is functioning optimally.
- Testkjøringer: Always perform test engravings on sample materials to fine-tune your settings before proceeding with the final project.
3.2 Real-Time Monitoring and Adjustments
During the engraving process:
- Monitor Temperature: Keep an eye on the material’s temperature to ensure it does not overheat.
- Adjust Settings on the Fly: If you observe signs of burning or carbonization, pause the process and adjust the power, Frekvens, or speed.
- Use Preview Functions: Many laser software packages offer real-time previews that help you predict the engraving outcome.
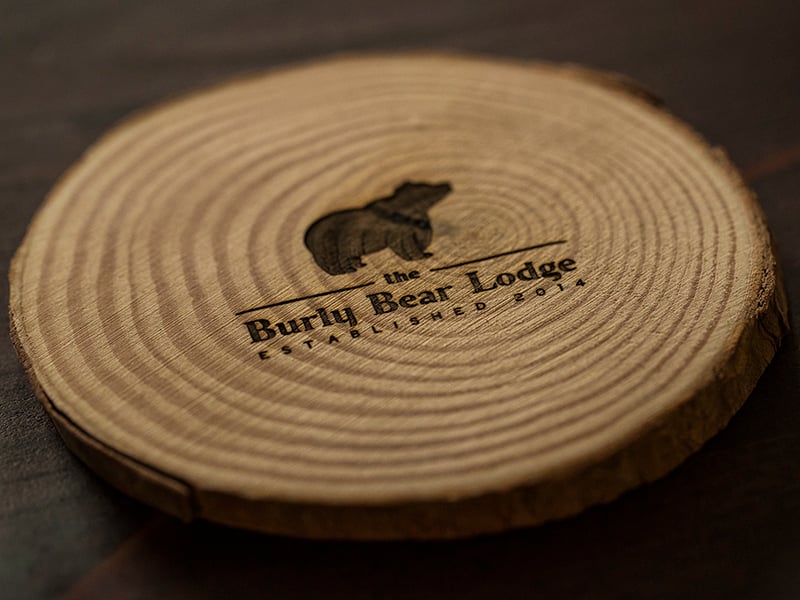
4. Optimal Settings for 10+ Materialer
Below are recommended laser power and frequency settings for preventing material carbonization across various materials. These settings serve as starting points and may need adjustments based on your specific machine and material variations.
4.1 Tre (Softwood & Hardwood)
- Makt: 50-70%
- Frekvens: 20-30 kHz
- Notater: Softwoods require lower power to prevent charring; hardwoods can tolerate slightly higher power due to denser structure.
4.2 Akryl (Klar & Colored)
- Makt: 60-80%
- Frekvens: 25-35 kHz
- Notater: Ensure the settings are optimized to avoid melting or excessive bubbling, especially on clear acrylic.
4.3 Lær
- Makt: 40-60%
- Frekvens: 15-25 kHz
- Notater: Lower power settings help maintain the natural texture without burning or excessive darkening.
4.4 Paper and Cardboard
- Makt: 30-50%
- Frekvens: 20-30 kHz
- Notater: Delicate materials like paper require minimal power to achieve clear, precise engravings without tearing.
4.5 Glass (With Coating or Backing)
- Makt: 40-60%
- Frekvens: 25-35 kHz
- Notater: When engraving glass, ensure proper cooling and consider using a backing material to diffuse heat.
4.6 Metall (Anodisert, Stainless, Aluminium)
- Makt: 70-90%
- Frekvens: 30-40 kHz
- Notater: Metals typically require higher power for deep, permanente markeringer, but ensure parameters prevent melting or warping.
4.7 Plast (ABS, Polykarbonat)
- Makt: 50-70%
- Frekvens: 25-35 kHz
- Notater: Optimize settings to prevent discoloration or deformation due to heat buildup.
4.8 Keramikk
- Makt: 30-50%
- Frekvens: 20-30 kHz
- Notater: Maintain lower power to avoid cracking or unwanted surface changes.
4.9 Gummi
- Makt: 40-60%
- Frekvens: 20-30 kHz
- Notater: Adjust settings to achieve clear markings without burning, especially for flexible or soft rubber materials.
4.10 Composite Materials
- Makt: 50-70%
- Frekvens: 25-35 kHz
- Notater: Fine-tuning is essential to accommodate varying material layers without causing uneven engraving.
4.11 Additional Materials
For any materials not listed, start at a mid-range power and frequency setting (omkring 60% makt, 25-30 kHz), then adjust based on test results.
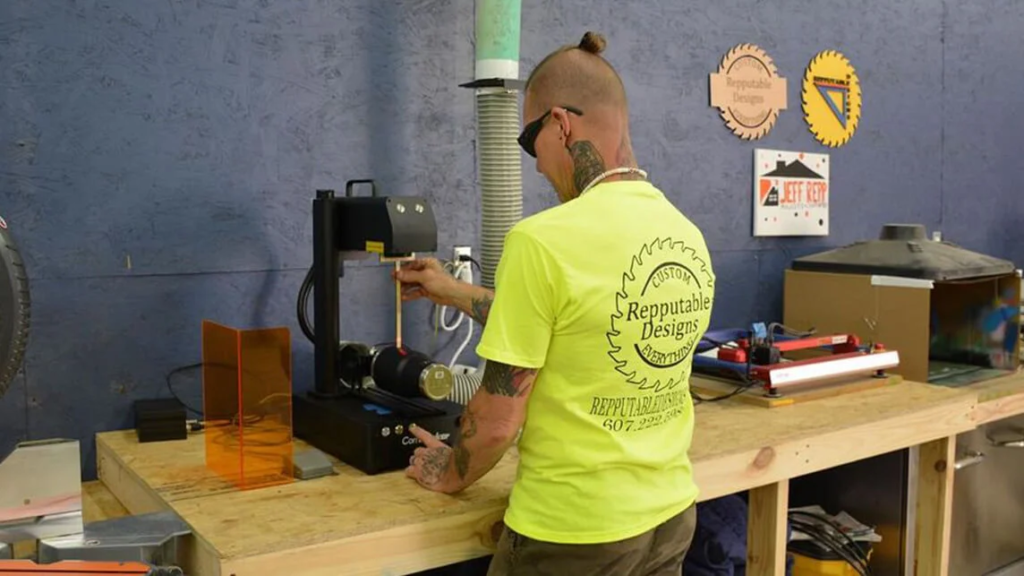
5. Tips and Best Practices
5.1 Fine-Tuning Through Test Patterns
Always run a test engraving using a standardized test pattern. This allows you to measure engraving depth and adjust settings incrementally until you achieve optimal results. Document your successful settings for future reference.
5.2 Maintaining Your Equipment
Regular maintenance is essential to ensure consistent performance:
- Clean Optics: Regularly clean the laser lens and mirrors.
- Check Cooling: Ensure the cooling system is working effectively.
- Programvareoppdateringer: Keep your engraving software updated to benefit from the latest calibration tools.
5.3 Environment and Safety
Maintain a stable environment for your laser engraver:
- Temperature: Keep the workspace within the recommended range to prevent thermal fluctuations.
- Ventilasjon: Ensure proper ventilation to dissipate heat and fumes.
- Sikkerhetsutstyr: Always wear laser safety goggles and follow manufacturer guidelines.
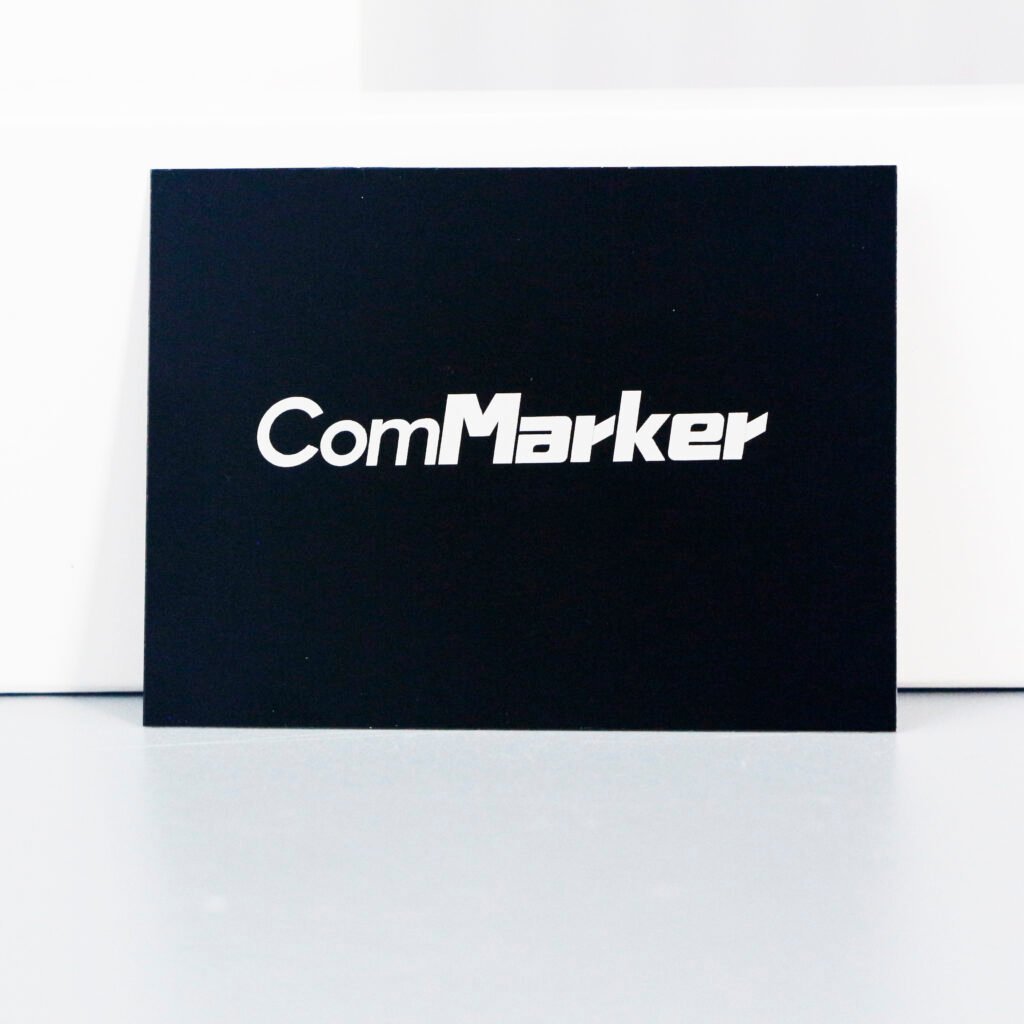
6. Casestudier i den virkelige verden
Casestudie 1: Fine Jewelry Engraving on Stainless Steel
An upscale jewelry manufacturer achieved exceptional detail on stainless steel components by fine-tuning their laser power to 75% and frequency to 35 kHz. Through careful calibration, they prevented material carbonization and produced micro-engraved patterns that met their stringent quality standards.
Casestudie 2: Customized Acrylic Signage
A small business specializing in custom acrylic signage implemented a 60% power and 30 kHz setting to produce high-contrast engravings without melting the material. Their consistent, high-quality results have helped reduce rework and improve customer satisfaction.
Casestudie 3: Industrial Marking on Aluminum
An industrial manufacturer needed deep, permanent markings on aluminum parts. They opted for a higher power setting of 85% with a frequency of 40 kHz, carefully calibrated to avoid warping the metal. The result was a robust, high-contrast engraving suitable for harsh operational environments.
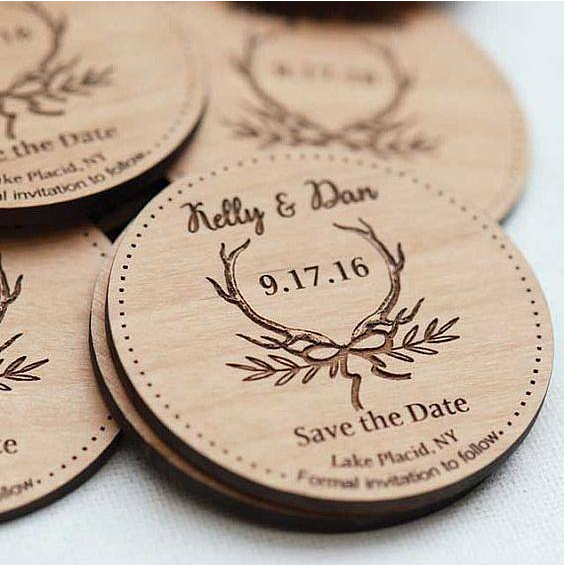
7. Preventing Engraving Burns and Material Carbonization
7.1 Preventing Engraving Burns
To prevent engraving burns, alltid:
- Lower the Power on Sensitive Materials: Use the minimal effective power settings for delicate or heat-sensitive materials.
- Adjust Frequency: Higher frequencies can help distribute the energy more evenly, reducing localized heat build-up.
- Monitor Real-Time: Continuously monitor the engraving process and adjust settings on the fly if overheating is detected.
7.2 Tips to Prevent Material Carbonization
- Pre-Test on Sample Materials: Always test settings on a sample before engraving the final product.
- Optimize Cooling: Ensure that the machine’s cooling system is operational, and consider additional ventilation if needed.
- Use Appropriate Passes: Instead of one high-power pass, use multiple passes at lower power to gradually achieve the desired depth without burning the material.
- Document and Adjust: Keep detailed records of the settings that work best for each material and make adjustments as needed over time.
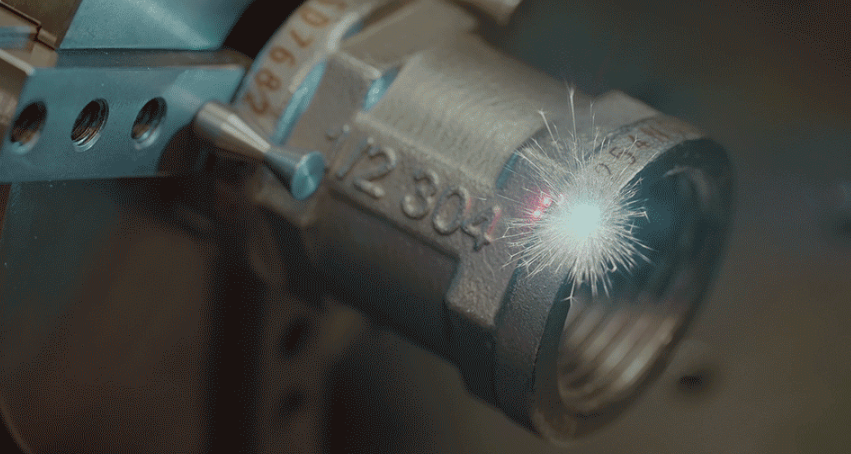
8. Advanced Techniques and Operational Best Practices
8.1 Multi-Pass Engraving for Optimal Depth
Employ multi-pass engraving to gradually build up the engraving depth. This technique minimizes the risk of carbonization by distributing the energy over several passes.
8.2 Overlapping Engraving for Enhanced Detail
For complex designs, overlapping engraving passes can help achieve a more uniform depth and prevent burnt edges. Use LightBurn’s preview tools to ensure consistency across overlapping areas.
8.3 Optimalisering av graveringsstier
Efficient path planning reduces machine wear and energy consumption. Utilize software optimization features to create the most direct engraving paths, minimizing unnecessary movement.
8.4 Real-Time Monitoring and Feedback
Invest in software tools that provide real-time feedback on engraving quality. Use these insights to make immediate adjustments, ensuring that every run meets the highest standards of quality without material carbonization.
9. Future Trends in Laser Engraving Settings
9.1 Smart Calibration Systems
The future of laser engraving will see the integration of AI-driven calibration systems that automatically adjust power, Frekvens, and speed settings in real time based on material feedback. This will further minimize the risk of carbonization and enhance overall efficiency.
9.2 Advanced Cooling and Energy Management
Innovations in cooling technology and energy management will reduce the thermal load on materials, enabling even higher precision and deeper engravings without burning.
9.3 Environmental and Sustainability Considerations
As industries move towards greener manufacturing practices, optimizing laser settings to reduce waste and energy consumption will be critical. Advanced software tools will help manufacturers achieve both high quality and sustainability.
10. Konklusjon
Achieving 0.001mm precision in laser engraving while preventing material carbonization is within reach when you fine-tune your laser power and frequency settings. By understanding the unique requirements of each material and adopting best practices such as multi-pass engraving and real-time monitoring, you can consistently produce high-quality, damage-free engravings.
Final Recommendations:
- For Delicate Materials: Start with lower power and higher frequency settings to minimize thermal impact.
- For Metals: Higher power settings are necessary, but balance them with controlled frequencies and multiple passes.
- Regular Calibration: Frequent testing and calibration are key to maintaining consistent results.
- Utilize Advanced Tools: Leverage real-time monitoring software and interactive material compatibility detectors to optimize your settings.
Invest in continuous learning and keep up with technological advancements to further refine your engraving process. With these strategies, you can effectively prevent engraving burns and material carbonization, ensuring every project achieves the highest level of precision and quality.
For more detailed technical specifications, further tutorials, and to explore our range of laser engraving solutions, please visit ComMarker.com or contact our expert support team at support@commarker.com.