La carbonización material durante el grabado láser es un desafío común que puede comprometer la calidad de su trabajo. Ya sea que estés marcando madera, acrílico, cuero, u otros materiales, La configuración láser incorrecta puede conducir a quemaduras no deseadas y acumulación de carbono, resultando en oscuro, desigual, o acabados degradados. En esta guía, Proporcionamos información procesable y configuraciones detalladas de energía y frecuencia de láser para Over 10 materiales. Nuestro objetivo es ayudarlo..
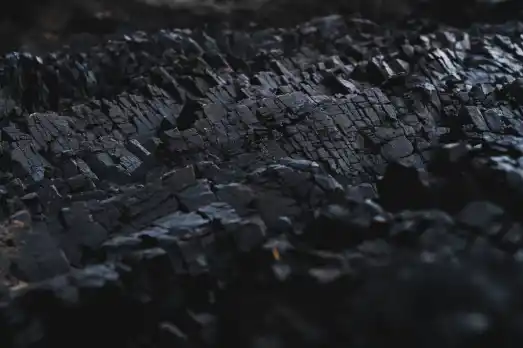
1. Comprender la carbonización material
1.1 ¿Qué es la carbonización material??
La carbonización del material es el proceso por el cual la superficie de un material se quema y se convierte en carbono. En grabado láser, Esto a menudo se manifiesta como un oscuro, área desigual donde el láser ha aplicado demasiada energía, conduciendo a ardor en lugar de cortar o marcar limpieza. Este resultado indeseable puede restar valor a la estética del producto final y afectar su durabilidad.
1.2 Causas comunes en el grabado láser
- Potencia láser excesiva: Cuando la salida del láser es demasiado alta, La energía puede quemar el material en lugar de grabarlo con precisión.
- Configuración de frecuencia incorrecta: La configuración de baja frecuencia puede concentrar la energía en un área pequeña, causando sobrecalentamiento.
- Enfriamiento insuficiente: La mala ventilación o los sistemas de enfriamiento inadecuados pueden conducir a una acumulación de calor.
- Sensibilidad al material: Algunos materiales son más propensos a la carbonización., Requerir un manejo delicado y configuraciones optimizadas.
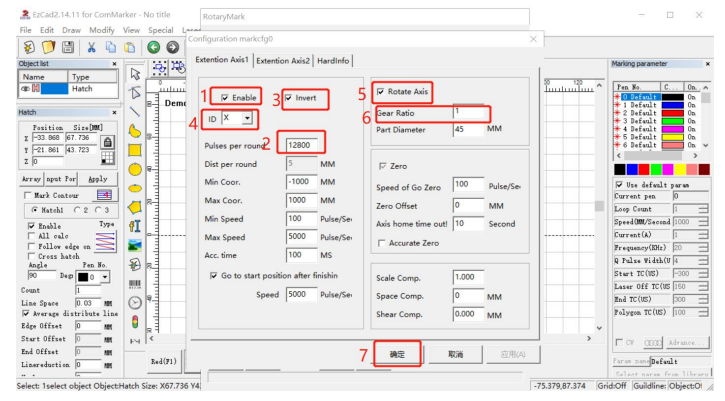
2. Fundamentos de la potencia láser y la configuración de frecuencia
2.1 Potencia del láser: Cómo afecta el grabado
potencia del láser, típicamente medido en vatios, determina la cantidad de energía entregada al material. Encontrar el equilibrio correcto es la clave:
- Menor potencia: Minimiza la acumulación de calor, Ideal para materiales delicados.
- Mayor poder: Permite un grabado más rápido y recortes más profundos, pero aumenta el riesgo de carbonización si no se maneja con cuidado.
2.2 Configuración de frecuencia y su papel
Frecuencia, medido en kilohertz (kilociclos), Influye con la frecuencia que los pulsos láser por segundo:
- Frecuencia alta: Proporciona un haz más continuo, conduciendo a un grabado más suave pero puede sobrecalentar materiales sensibles si no se controla.
- Baja frecuencia: Reduce la entrada de energía general, Lo cual es beneficioso para prevenir la carbonización, pero puede dar lugar a velocidades de procesamiento más lentas.
Equilibrar la potencia y la frecuencia es crucial para lograr la limpieza, grabados precisos sin quemaduras no deseadas.
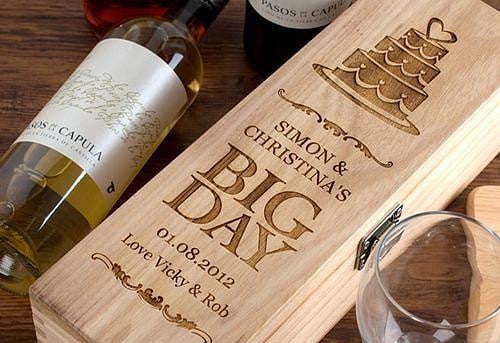
3. Prevención de quemaduras de grabado: Mejores prácticas
3.1 Preparación previa a la gestión
La preparación adecuada es esencial para prevenir la carbonización material:
- Inspección de material: Asegúrese de que el material esté limpio, libre de contaminantes, y correctamente asegurado.
- Verificación del sistema de enfriamiento: Verifique que el sistema de enfriamiento de su grabador de láser funcione de manera óptima.
- Ejecuciones de prueba: Siempre realice grabados de prueba en materiales de muestra para ajustar su configuración antes de continuar con el proyecto final.
3.2 Monitoreo y ajustes en tiempo real
Durante el proceso de grabado:
- Temperatura de monitor: Esté atento a la temperatura del material para asegurarse de que no se sobrecaliente.
- Ajustar la configuración de la mosca: Si observa signos de quema o carbonización, Pausa el proceso y ajuste la potencia, frecuencia, o velocidad.
- Utilizar funciones de vista previa: Muchos paquetes de software láser ofrecen vistas previas en tiempo real que lo ayudan a predecir el resultado del grabado.
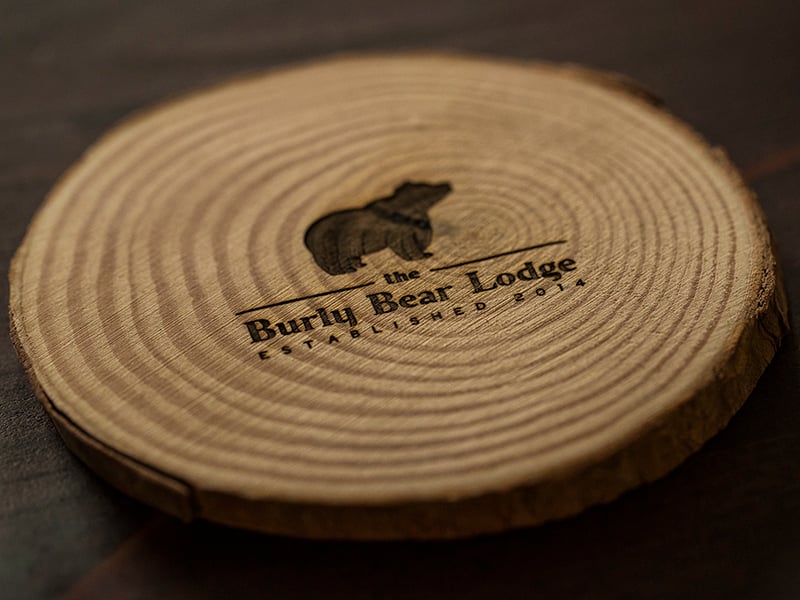
4. Configuración óptima para 10+ Materiales
A continuación se recomiendan la potencia del láser y la configuración de frecuencia para prevenir la carbonización del material en varios materiales. Estas configuraciones sirven como puntos de partida y pueden necesitar ajustes basados en su máquina específica y variaciones de material.
4.1 Madera (Madera blanda & Madera dura)
- Fuerza: 50-70%
- Frecuencia: 20-30 kilociclos
- Notas: Las maderas blandas requieren una menor potencia para evitar el carbono; Las maderas duras pueden tolerar una potencia ligeramente mayor debido a la estructura más densa.
4.2 Acrílico (Claro & De colores)
- Fuerza: 60-80%
- Frecuencia: 25-35 kilociclos
- Notas: Asegúrese de que la configuración esté optimizada para evitar fusión o burbujeo excesivo, especialmente en acrílico claro.
4.3 Cuero
- Fuerza: 40-60%
- Frecuencia: 15-25 kilociclos
- Notas: Configuración de potencia más baja ayudan a mantener la textura natural sin quemar o oscurecer excesivo.
4.4 Papel y cartón
- Fuerza: 30-50%
- Frecuencia: 20-30 kilociclos
- Notas: Los materiales delicados como el papel requieren una potencia mínima para lograrlo., grabados precisos sin rasgaduras.
4.5 Vaso (Con recubrimiento o respaldo)
- Fuerza: 40-60%
- Frecuencia: 25-35 kilociclos
- Notas: Al grabar vidrio, Asegure un enfriamiento adecuado y considere usar un material de respaldo para difundir el calor.
4.6 Metal (Anodizado, Inoxidable, Aluminio)
- Fuerza: 70-90%
- Frecuencia: 30-40 kilociclos
- Notas: Los metales generalmente requieren una mayor potencia para las profundidades, marcas permanentes, pero asegúrese de que los parámetros eviten la fusión o deformación.
4.7 El plastico (abdominales, policarbonato)
- Fuerza: 50-70%
- Frecuencia: 25-35 kilociclos
- Notas: Optimizar la configuración para evitar la decoloración o la deformación debido a la acumulación de calor.
4.8 Cerámica
- Fuerza: 30-50%
- Frecuencia: 20-30 kilociclos
- Notas: Mantenga una menor potencia para evitar los cambios de la superficie no deseados o no deseados.
4.9 Goma
- Fuerza: 40-60%
- Frecuencia: 20-30 kilociclos
- Notas: Ajuste la configuración para lograr marcas claras sin quemarse, Especialmente para materiales de caucho flexible o suave.
4.10 Materiales compuestos
- Fuerza: 50-70%
- Frecuencia: 25-35 kilociclos
- Notas: El ajuste fino es esencial para acomodar capas de material variables sin causar grabado desigual.
4.11 Materiales adicionales
Para cualquier material que no esté en la lista, Comience en una configuración de energía y frecuencia de rango medio (alrededor 60% fuerza, 25-30 kilociclos), Luego ajuste según los resultados de las pruebas.
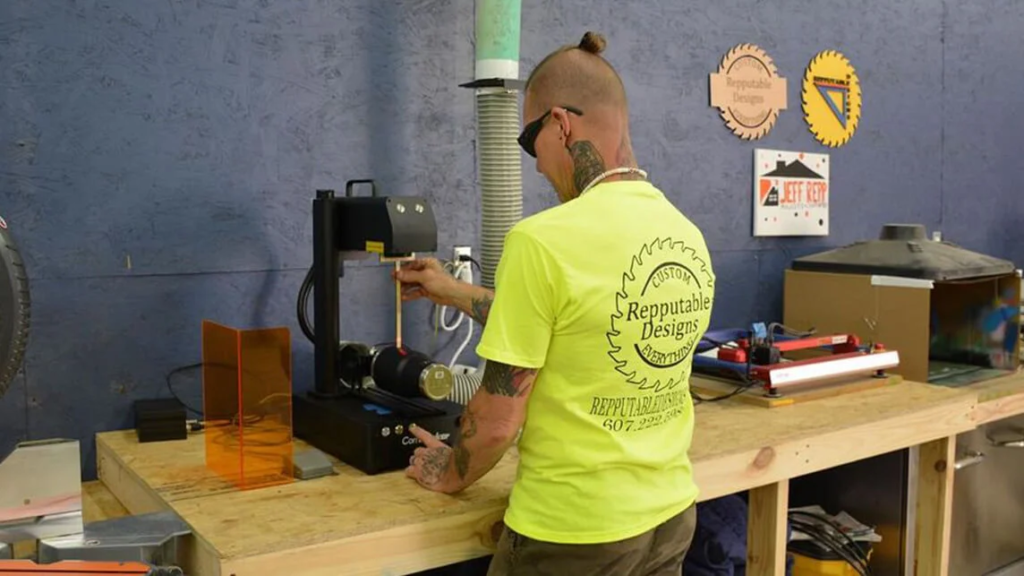
5. Consejos y mejores prácticas
5.1 Ajuste fino a través de patrones de prueba
Siempre ejecute un grabado de prueba utilizando un patrón de prueba estandarizado. Esto le permite medir la profundidad de grabado y ajustar la configuración de forma incremental hasta que obtenga resultados óptimos. Documente su configuración exitosa para referencia futura.
5.2 Mantener su equipo
El mantenimiento regular es esencial para garantizar un rendimiento constante:
- Óptica limpia: Limpie regularmente la lente y los espejos.
- Verifique el enfriamiento: Asegúrese de que el sistema de enfriamiento funcione de manera efectiva.
- Actualizaciones de software: Mantenga su software de grabado actualizado para beneficiarse de las últimas herramientas de calibración.
5.3 Medio ambiente y seguridad
Mantener un entorno estable para su grabador láser:
- Temperatura: Mantenga el espacio de trabajo dentro del rango recomendado para evitar fluctuaciones térmicas.
- Ventilación: Asegure una ventilación adecuada para disipar el calor y los humos.
- Equipo de seguridad: Siempre use gafas de seguridad láser y siga las pautas del fabricante.
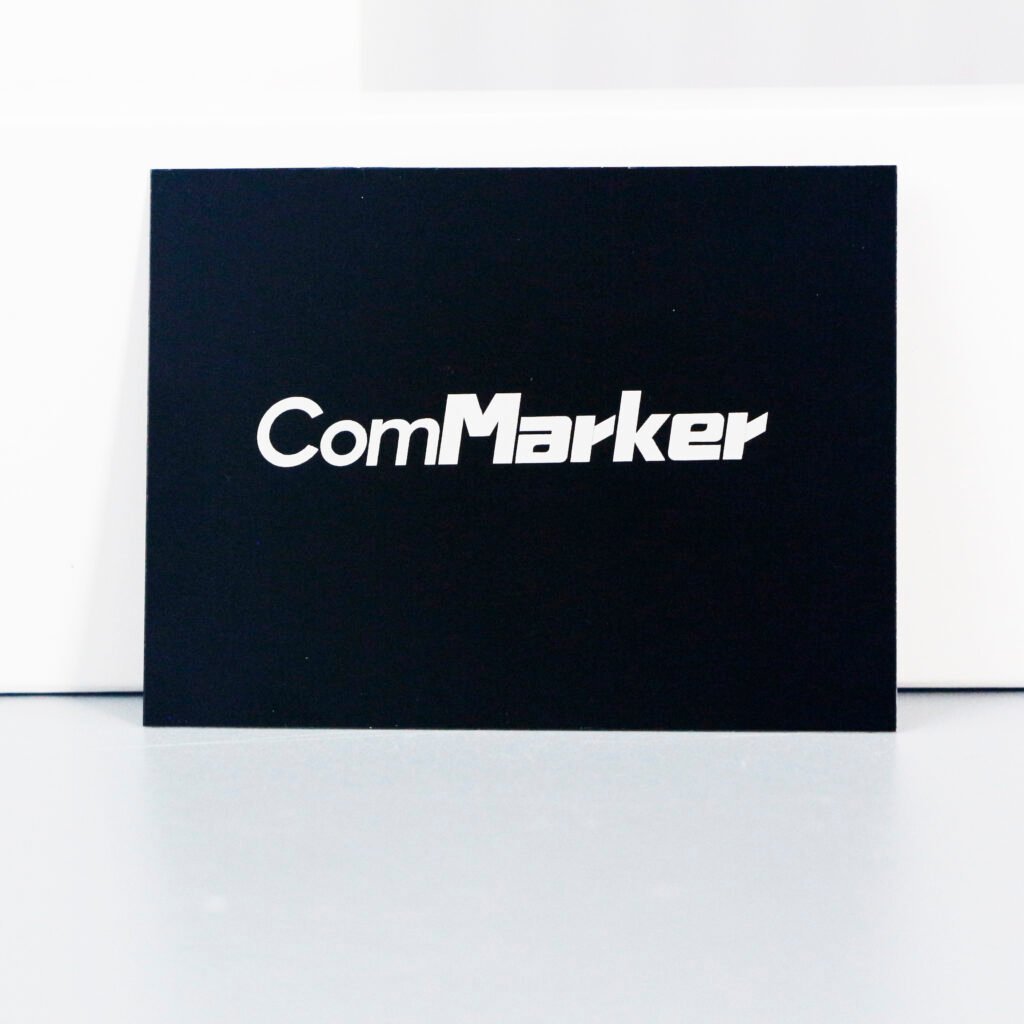
6. Estudios de casos del mundo real
Caso de estudio 1: Grabado de joyería fina en acero inoxidable
Un fabricante de joyería exclusivo logró detalles excepcionales en los componentes de acero inoxidable al ajustar su potencia láser a 75% y frecuencia a 35 kilociclos. A través de una calibración cuidadosa, Prevenieron la carbonización del material y produjeron patrones micrograbados que cumplieron con sus estrictos estándares de calidad..
Caso de estudio 2: Señalización acrílica personalizada
Una pequeña empresa especializada en señalización acrílica personalizada implementó un 60% poder y 30 Configuración de KHz para producir grabados de alto contraste sin derretir el material. Su consistente, Los resultados de alta calidad han ayudado a reducir el retrabajo y mejorar la satisfacción del cliente.
Caso de estudio 3: Marcado industrial sobre aluminio
Un fabricante industrial necesitaba profundo, Marcas permanentes en piezas de aluminio. Optaron por una configuración de mayor potencia de 85% con una frecuencia de 40 kilociclos, Calibrado cuidadosamente para evitar deformar el metal. El resultado fue un robusto, Grabado de alto contraste adecuado para entornos operativos duros.
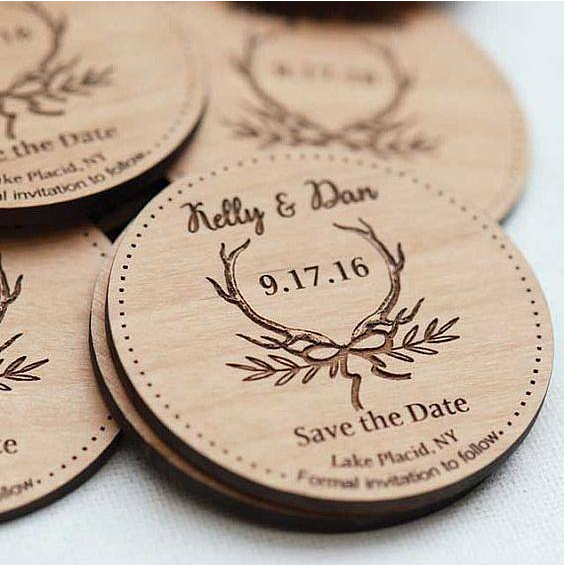
7. Prevención de quemaduras de grabado y carbonización material
7.1 Prevención de quemaduras de grabado
Para evitar el grabado quemaduras, siempre:
- Reducir la alimentación de materiales sensibles: Utilice la configuración de potencia efectiva mínima para materiales delicados o sensibles al calor.
- Ajustar la frecuencia: Las frecuencias más altas pueden ayudar a distribuir la energía de manera más uniforme, Reducción de la acumulación de calor localizado.
- Monitorear en tiempo real: Controle continuamente el proceso de grabado y ajuste la configuración de la mosca si se detecta sobrecalentamiento.
7.2 Consejos para evitar la carbonización del material
- Prueba previa en materiales de muestra: Siempre pruebe la configuración de una muestra antes de grabar el producto final.
- Optimizar el enfriamiento: Asegúrese de que el sistema de enfriamiento de la máquina esté operativo, y considere ventilación adicional si es necesario.
- Use pases apropiados: En lugar de un pase de alta potencia, Use múltiples pases a menor potencia para lograr gradualmente la profundidad deseada sin quemar el material.
- Documentar y ajustar: Mantenga registros detallados de la configuración que funcione mejor para cada material y haga ajustes según sea necesario con el tiempo.
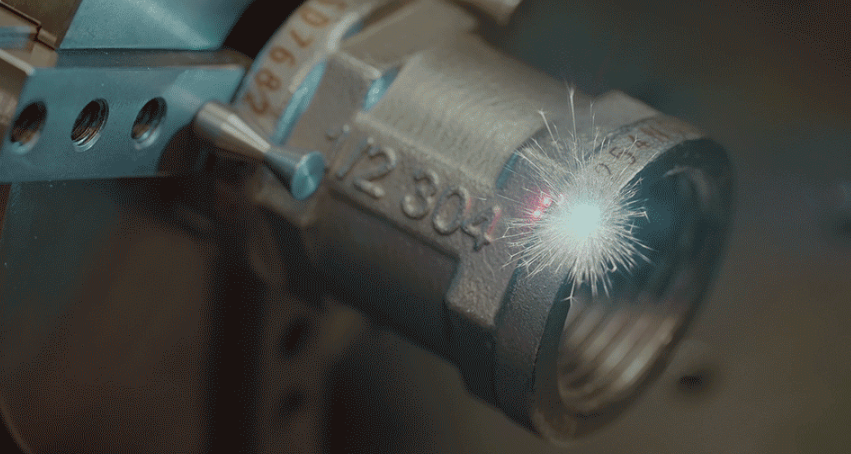
8. Técnicas avanzadas y mejores prácticas operativas
8.1 Grabado múltiple para una profundidad óptima
Emplear el grabado multipass para construir gradualmente la profundidad de grabado. Esta técnica minimiza el riesgo de carbonización al distribuir la energía en varios pases.
8.2 Grabado superpuesto para detalles mejorados
Para diseños complejos, Los pases de grabado superpuesto pueden ayudar a lograr una profundidad más uniforme y evitar los bordes quemados. Use las herramientas de vista previa de Lightburn para garantizar la consistencia en las áreas superpuestas.
8.3 Optimización de rutas de grabado
La planificación eficiente de la ruta reduce el desgaste de la máquina y el consumo de energía. Utilice funciones de optimización de software para crear las rutas de grabado más directas, minimizando el movimiento innecesario.
8.4 Monitoreo y retroalimentación en tiempo real
Invierta en herramientas de software que proporcionen comentarios en tiempo real sobre la calidad del grabado. Use estas ideas para realizar ajustes inmediatos, Asegurar que cada ejecución cumpla con los más altos estándares de calidad sin carbonización material.
9. Tendencias futuras en la configuración de grabado láser
9.1 Sistemas de calibración inteligente
El futuro del grabado láser verá la integración de los sistemas de calibración impulsados por la IA que ajustan automáticamente la energía, frecuencia, y configuración de velocidad en tiempo real según la retroalimentación del material. Esto minimizará aún más el riesgo de carbonización y mejorará la eficiencia general..
9.2 Refriamiento avanzado y gestión de energía
Innovaciones en tecnología de enfriamiento y gestión de energía reducirán la carga térmica en los materiales, habilitando una precisión aún mayor y grabados más profundos sin quemarse.
9.3 Consideraciones ambientales y de sostenibilidad
A medida que las industrias se mueven hacia prácticas de fabricación más ecológicas, La optimización de la configuración del láser para reducir el consumo de residuos y energía será fundamental. Las herramientas de software avanzadas ayudarán a los fabricantes a alcanzar la alta calidad y la sostenibilidad.
10. Conclusión
Lograr una precisión de 0.001 mm en el grabado con láser mientras evita la carbonización del material está al alcance cuando ajusta la configuración de energía y frecuencia de su láser. Al comprender los requisitos únicos de cada material y la adopción de las mejores prácticas, como el grabado de múltiples pasos y el monitoreo en tiempo real., puedes producir constantemente de alta calidad, grabados sin daños.
Recomendaciones finales:
- Para materiales delicados: Comience con una menor potencia y una mayor configuración de frecuencia para minimizar el impacto térmico.
- Para metales: Se necesitan configuraciones de mayor potencia, pero equilibrarlos con frecuencias controladas y múltiples pases.
- Calibración regular: Las pruebas y la calibración frecuentes son clave para mantener resultados consistentes.
- Utilizar herramientas avanzadas: Aprovechar el software de monitoreo en tiempo real y los detectores de compatibilidad de material interactivo para optimizar su configuración.
Invierta en el aprendizaje continuo y mantenga el ritmo de los avances tecnológicos para refinar aún más su proceso de grabado. Con estas estrategias, Puede evitar efectivamente las quemaduras de grabado y la carbonización del material., Asegurar que cada proyecto logre el más alto nivel de precisión y calidad.
Para especificaciones técnicas más detalladas, Tutoriales adicionales, y para explorar nuestra gama de soluciones de grabado láser, por favor visita ComMarker.com o comuníquese con nuestro equipo de apoyo experto en soporte@commarker.com.