La réalisation de la précision au niveau du micron dans la gravure laser change la donne pour les entreprises et les professionnels qui exigent une qualité sans compromis. Dans ce guide, Nous explorerons des techniques d'étalonnage avancées spécialement conçues pour les gêneurs de communes pour vous aider à atteindre une précision de 0,001 mm. Que vous soyez concentré sur le marquage industriel complexe, produits personnalisés haut de gamme, ou créations artistiques personnalisées, L'étalonnage précis est le fondement de l'excellence.
Dans cet article complet, Nous couvrirons la science derrière l'étalonnage, techniques étape par étape, Dépannage des problèmes communs, et les meilleures pratiques pour l'entretien à long terme. Notre objectif est de fournir des informations exploitables qui améliorent votre processus d'étalonnage du graveur laser, ensuring consistent, des résultats de haute qualité à chaque fois.
1.1 The Importance of Laser Engraver Calibration
Laser engraver calibration is crucial to ensuring that your machine delivers optimal performance and achieves the highest possible level of precision. Without proper calibration, even the best laser engraver can fall short of delivering consistent results. For ComMarker users, achieving a precision of 0.001mm means that every detail, no matter how minute, is captured accurately—this is essential for high-end industrial marking and artistic engraving.
Calibration not only improves quality but also extends the lifespan of your equipment by ensuring that the laser beam is properly aligned and focused. Consistent calibration practices can reduce wear and tear on mechanical components, minimize errors, et vous aider à atteindre la précision au niveau du micron dans chaque projet.
1.2 Comprendre la précision au niveau du micron
Précision au niveau du micron (0.001millimètre) est une mesure de précision qui est particulièrement importante dans les applications nécessitant des détails complexes. Dans des industries comme l'électronique, aérospatial, et des bijoux, Même la plus petite déviation peut affecter considérablement la fonctionnalité ou la qualité esthétique d'un produit. Atteindre ce niveau de précision nécessite un étalonnage méticuleux du point focal du laser, alignement de faisceau, et paramètres de fonctionnement.
Avec des techniques d'étalonnage avancées, Les gênants du Commarker peuvent régulièrement livrer ces normes élevées, S'assurer que chaque gravure est aussi parfaite que la dernière. Dans ce guide, Nous vous guiderons à travers les étapes nécessaires pour atteindre une telle précision, en mettant l'accent sur l'étalonnage du graveur laser et la précision du niveau de micron.
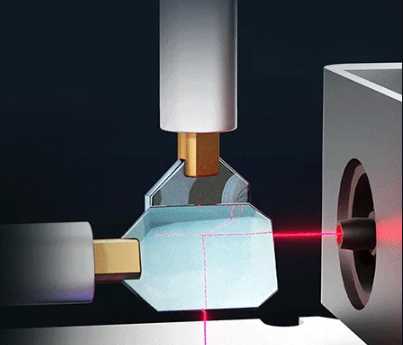
2. Fondamentaux de l'étalonnage du graveur au laser
2.1 Qu'est-ce que l'étalonnage?
L'étalonnage est le processus d'alignement et d'ajustement des composants d'un graveur laser pour s'assurer qu'il fonctionne dans ses tolérances spécifiées. Cela implique un réglage fin de la focalisation du faisceau laser, alignement, paramètres d'alimentation, et la vitesse, de sorte que la gravure finale correspond exactement à la conception numérique. L'étalonnage régulier est essentiel pour maintenir la cohérence, en particulier dans les environnements où même des écarts mineurs peuvent entraîner des problèmes de qualité importants.
2.2 Paramètres d'étalonnage clés
Les paramètres clés qui nécessitent l'étalonnage incluent:
- Distance focale: Assurer que le faisceau laser est parfaitement axé sur la surface du matériau.
- Alignement de faisceau: Ajustement des miroirs et des optiques pour maintenir un, poutre uniforme.
- Paramètres d'alimentation: Calibrage de la puissance laser pour éviter une surexposition ou une sous-exposition.
- Gravure vitesse et fréquence: Équilibrage de la vitesse avec la qualité pour atteindre une profondeur et une résolution cohérentes.
- Intervalle de ligne et DPI: Assurer que l'espacement entre les lignes laser (et résolution globale) est réglé pour atteindre la précision au niveau micron.
2.3 Outils et équipements nécessaires
Pour effectuer un étalonnage avancé sur votre graveur de communes, tu auras besoin:
- Soleuse d'étalonnage / modèle: Un outil de haute précision pour mesurer les distances.
- Micromètre: Pour vérifier les différences infimes dans les dimensions.
- Lunettes de sécurité: Essentiel pour protéger vos yeux pendant le fonctionnement du laser.
- Logiciel d'étalonnage: Outils intégrés dans Lightburn ou EZCAD2 qui permettent des ajustements précis.
- Produits de nettoyage: Alcool isopropylique, tissus sans peluches, et les kits de nettoyage des lentilles pour garder l'optique exempte de poussière et de débris.
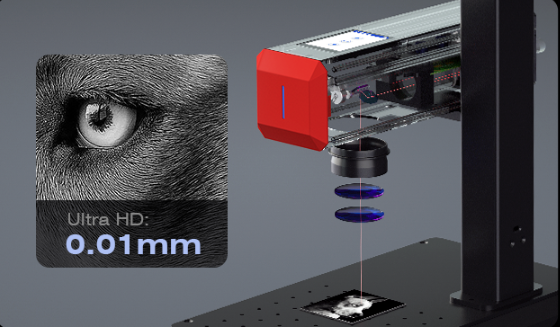
3. Techniques d'étalonnage avancées pour les graveurs des commandants
3.1 Configuration pré-calibration et contrôle de l'environnement
Avant de commencer le processus d'étalonnage, Il est essentiel de préparer votre espace de travail:
- Surface stable: Assurez-vous que le graveur est placé sur une stable, surface sans vibration.
- Température et humidité: Maintenir des conditions environnementales optimales. Les graveurs des commandants fonctionnent généralement le mieux dans une plage de température de 0 ° C à 28 ° C et l'humidité en dessous 70%.
- Optique propre: Nettoyez la tête laser, miroirs, et lentilles pour éliminer toute poussière ou résidu qui peut affecter la qualité du faisceau.
3.2 Processus d'étalonnage du graveur laser étape par étape
Suivez ces étapes détaillées pour calibrer votre graveur de communes pour une précision de 0,001 mm:
- La configuration initiale:
- Allumez votre graveur de communes et lancez votre logiciel d'étalonnage (par exemple., Lightburn ou Ezcad2).
- Assurez-vous que toutes les pièces mécaniques sont sécurisées et que l'espace de travail est propre.
- Ajustement focal:
- Utilisez le système de mise au point en deux feuilles rouges pour aligner le faisceau laser avec le modèle d'étalonnage.
- Ajustez lentement la focus. Cela indique le point focal optimal.
- Verrouiller les paramètres de mise au point une fois atteint.
- Alignement de faisceau:
- Activer le laser à un réglage de faible puissance.
- Diriger le faisceau laser sur une cible d'étalonnage marquée.
- Réglez manuellement les miroirs du galvanomètre jusqu'à ce que le faisceau soit centré et uniforme sur la cible.
- Vérifiez l'alignement à plusieurs points à travers la zone de gravure pour assurer la cohérence.
- Étalonnage de puissance:
- Réglez le laser sur la puissance recommandée (par exemple., 75% Pour le Commarker B4-20W).
- Graver un modèle de test sur un matériau d'échantillonnage.
- Mesurez la profondeur de gravure à l'aide d'un micromètre et ajustez les paramètres de puissance pour obtenir des résultats cohérents à travers le motif.
- Étalonnage de vitesse et de fréquence:
- Configurer la vitesse de gravure (par exemple., 1000 mm/sec) et fréquence (par exemple., 30 kHz).
- Exécutez une gravure de test et observez la qualité. Si la gravure semble inégale ou trop peu profonde, ajuster ces paramètres progressivement.
- Répétez le test jusqu'à ce que la gravure soit uniforme et répond aux spécifications souhaitées.
- Intervalle de ligne et ajustement DPI:
- Définir l'intervalle de ligne (par exemple., 0.025millimètre) et dpi (par exemple., 1000) Pour assurer une résolution fine.
- Graver un modèle détaillé et examiner la cohérence inter-lignes. Ajuster si nécessaire pour éviter les chevauchements ou les lacunes.
- Angle de gravure et passe:
- Expérimentez l'angle de gravure (par exemple., 45°) Pour améliorer l'effet 2.5D.
- Déterminer le nombre optimal de passes (par exemple., 100) requis pour atteindre la profondeur de gravure souhaitée sans compromettre les détails.
- Documenter les paramètres pour référence future.
3.3 Utilisation de modèles de test pour un réglage fin
Implémentez les modèles de test spécialement conçus pour l'étalonnage:
- Motifs de grille: Graver un motif de grille pour vérifier l'uniformité en profondeur et espacement de gravure.
- Schémas de dégradé: Utilisez des modèles de gradient de gris pour évaluer l'effet 2.5D et assurer des transitions en douceur entre différentes profondeurs.
- Texte et ridules: Graver un exemple de texte ou de conception de ligne complexe pour évaluer la précision et les détails au niveau du micron.
3.4 Réglage de la distance focale et de l'alignement du faisceau
La distance focale est essentielle pour obtenir une précision de 0,001 mm:
- Double technique de la lumière rouge: Utilisez la méthode de chevauchement de la lumière rouge pour obtenir le foyer optimal.
- Ajustements manuels: Affiner le focus manuellement, faire de petits ajustements incrémentiaux et des tests après chaque changement.
- Répétabilité: Assurez-vous que le point focal est cohérent à chaque fois en exécutant plusieurs gravures d'essai et en comparant les résultats.
3.5 Calibration du logiciel dans Lightburn et Ezcad2
Lightburn et Ezcad2 fournissent des outils intégrés pour l'étalonnage:
- Importer des fichiers d'étalonnage: Utilisez le fichier d'étalonnage du fabricant pour définir les paramètres de base.
- Réglage des paramètres: Modifier les paramètres tels que DPI, intervalle de ligne, et passer le nombre directement dans le logiciel.
- Aperçu en temps réel: Utilisez la fonction d'aperçu de Lightburn pour voir une gravure simulée avant de démarrer le processus réel. Ajustez les paramètres en fonction de l'aperçu pour affiner la précision.
- Économiser des profils: Une fois que des paramètres optimaux sont obtenus, Enregistrez la configuration en tant que profil personnalisé pour des résultats cohérents dans les projets futurs.
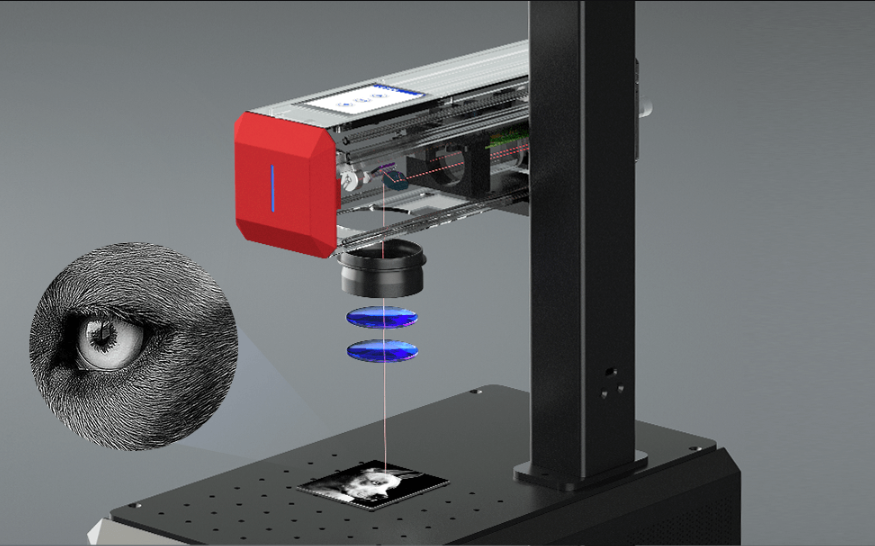
4. Dépannage et optimisation pour la précision au niveau du micron
4.1 Problèmes d'étalonnage communs et leurs solutions
Problème: Profondeur de gravure incohérente
- Solution: Revisez l'étalonnage de la mise au point en utilisant la double méthode rouge-lumière et assurez-vous que le modèle d'étalonnage est correctement aligné. Vérifiez que les conditions environnementales (température et humidité) sont dans la plage recommandée.
Problème: Gravure floue ou inégale
- Solution: Ajuster les paramètres du laser et des paramètres de fréquence. Augmenter le nombre de passes si nécessaire, et ré-calibre l'alignement du faisceau pour assurer l'uniformité dans la zone de travail.
Problème: La dérive de l'équipement dans le temps
- Solution: Planifier des séances d'étalonnage régulières. Documenter les paramètres d'étalonnage et les comparer périodiquement pour détecter toute dérive des performances. Entretien régulier, y compris le nettoyage des composants optiques, est essentiel.
4.2 Maintenir un étalonnage cohérent dans le temps
La cohérence à long terme nécessite une approche structurée:
- Chèques quotidiens: Effectuer une inspection visuelle rapide du faisceau laser et des paramètres de mise au point au début de chaque journée.
- Étalonnage hebdomadaire: Exécuter une routine d'étalonnage complète chaque semaine, surtout si la machine est utilisée en continu.
- Journaux de maintenance: Gardez des enregistrements détaillés des paramètres d'étalonnage, Résultats des tests, et tous les ajustements effectués. Cette documentation aide à identifier les tendances et à résoudre de manière préventive.
4.3 Exemples du monde réel et études de cas
Plusieurs utilisateurs des commandants ont réussi à atteindre une précision au niveau du micron:
- Étude de cas: Un fabricant d'électronique a obtenu une précision de 0,001 mm sur les gravures PCB en mettant en œuvre une routine d'étalonnage hebdomadaire stricte et en utilisant des modèles de test de grille détaillés. Leur processus d'étalonnage cohérent a réduit les problèmes de désalignement et l'amélioration de la qualité du produit par 25%.
- Commentaires des clients: «Depuis l'adoption des techniques d'étalonnage avancées décrites dans ce guide, Notre rendement de production a considérablement augmenté, Et la précision de nos gravures est désormais deuxième,»Dit un utilisateur de commissaire de longue date dans l'industrie automobile.
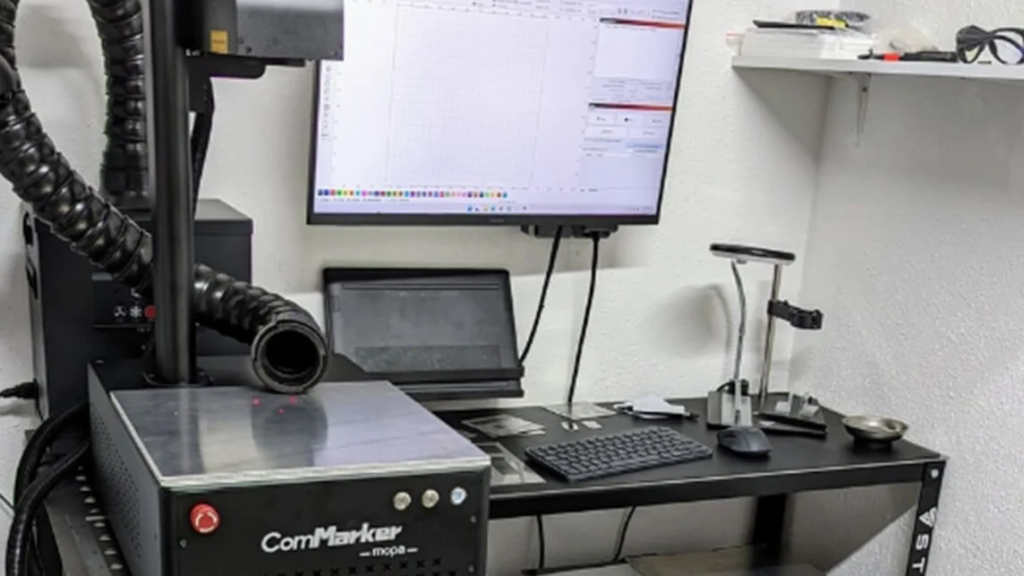
5. Meilleures pratiques et conseils professionnels
5.1 Établir un calendrier d'étalonnage de routine
- Tous les jours: Inspection rapide et vérification des points focaux.
- Hebdomadaire: Étalonnage complet à l'aide de modèles de test détaillés.
- Mensuel: Examen complet des paramètres et ajustement de toute dérive dans le système.
5.2 Paramètres d'étalonnage documentés et révise
- Créer un journal d'étalonnage: Enregistrez tous les paramètres et les résultats des tests.
- Analyser les tendances: Revoir régulièrement les journaux pour identifier les modifications ou les incohérences progressives.
- Ajuster de manière proactive: Utilisez les données pour ajuster les paramètres de manière préventive avant que des problèmes importants ne surviennent.
5.3 Optimisez votre environnement
- Contrôle de la température: Assurez-vous que votre espace de travail est maintenu à une température cohérente (idéalement entre 10 ° C et 28 ° C).
- Humidité: Gardez l'humidité en dessous 70% Pour éviter tout impact sur les performances laser.
- Surface stable: Placez votre graveur laser sur une surface sans vibration pour éviter toute interférence pendant le processus d'étalonnage.
5.4 Tirer parti de la communauté et du soutien du fabricant
- Rejoignez des forums: Engagez-vous avec les communautés en ligne axées sur l'étalonnage et la maintenance du graveur au laser.
- Ressources du fabricant: Utiliser les manuels d'utilisation, tutoriels vidéos, et le support technique offert par Commarker.
- Boucle de rétroaction: Partagez vos résultats d'étalonnage et apprenez des expériences des autres pour améliorer continuellement vos techniques.
6. Conclusion
Obtenir une précision de 0,001 mm avec votre graveur de laser Commarker est un processus qui exige une attention méticuleuse aux détails d'étalonnage. En suivant les techniques d'étalonnage avancées - en allant à partir de réglages précis de la longueur focale à l'optimisation détaillée des paramètres dans Lightburn - vous pouvez vous assurer que chaque gravure est exécutée avec une précision au niveau micron.
Points clés à retenir:
- Étalonnage du graveur laser est essentiel pour maintenir une haute précision et une cohérence dans votre travail.
- Utilisation d'outils avancés et de fonctionnalités logicielles, comme le mode Slice 3D de Lightburn, vous permet de traduire efficacement les données en niveaux de gris en profondeur de gravure variable.
- Entretien régulier, documentation approfondie, et les ajustements proactifs sont essentiels pour maintenir les performances au fil du temps.
- Inglissez avec la communauté et tirez parti du support du fabricant pour des améliorations et dépannage continu.
Dernières pensées:
La précision est la caractéristique de la qualité dans la gravure laser. Avec ces techniques d'étalonnage avancées, Vous êtes équipé pour atteindre une précision exceptionnelle dans chaque projet, Que vous marquiez des composants électroniques délicats ou que vous produisiez des conceptions personnalisées haut de gamme. Le voyage vers une précision de 0,001 mm nécessite un apprentissage continu, étalonnage régulier, et un engagement envers l'excellence.
Pour plus de détails, ressources techniques, et soutien personnalisé, veuillez visiter Commarker.com ou contactez notre équipe d'experts à support@commarker.com. Maîtriser l'art de laser engraver calibration and unlock the full potential of your machine to achieve true micron-level accuracy.