1.1 The Evolving Landscape of Laser Technology
In today’s fast-paced industrial and creative markets, laser technology has become indispensable. From intricate engraving to high-speed marking, lasers have revolutionized manufacturing, healthcare, électronique, and even art. As we advance further into 2025, we witness unprecedented innovations that promise to redefine precision processing. With increasing demand for customization, qualité, et efficacité, understanding the intricacies of laser systems is crucial for businesses and individuals alike.
Laser systems come in various forms, each designed to meet specific operational needs. Two of the most prominent technologies in this realm are Galvo lasers and Fiber lasers. While both have their unique strengths, they serve different purposes and excel in various applications. De plus, the emergence of cutting-edge technologies like 3D UV Galvo is pushing the boundaries of what is possible in laser processing.
1.2 Why Compare Galvo and Fiber Lasers?
As businesses consider investments in laser technology, a common question arises: “What is the difference between Galvo and Fiber Laser?” Each technology offers distinct advantages based on application, précision, vitesse, and material compatibility. Galvo systems are celebrated for their rapid scanning capabilities and are often the preferred choice for high-speed marking and engraving, especially on flat surfaces. En revanche, Fiber lasers are renowned for their ability to deliver high power and precise marking on metals and other robust materials.
Understanding the differences between these two laser systems can help you choose the right equipment for your specific needs, ensuring that you maximize efficiency, réduire les temps d'arrêt, and achieve superior quality in your production processes.
1.3 Introducing 3D UV Galvo: A New Frontier
In the midst of these established technologies, 3D UV Galvo has emerged as a groundbreaking innovation. This technology combines the rapid scanning ability of Galvo systems with the unique benefits of UV lasers, resulting in a laser system that is capable of achieving incredibly high precision in three-dimensional space. With its ability to process complex surfaces and create detailed 3D engravings, 3D UV Galvo is setting new benchmarks in laser processing technology. As we explore the differences between Galvo and Fiber lasers, we will pay special attention to how 3D UV Galvo technology is revolutionizing the field.
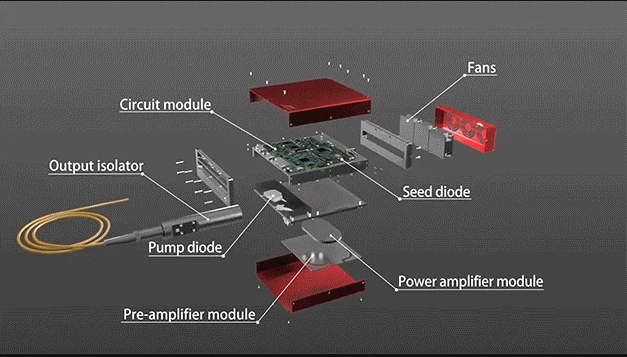
2. Comprendre la technologie de gravure au laser
2.1 The Science Behind Laser Technology
En son coeur, laser technology is all about emitting a concentrated beam of light with high energy and coherence. The term “laser” stands for “Light Amplification by Stimulated Emission of Radiation.” Lasers are unique in that they emit light at a specific wavelength, which can be finely tuned for various applications. This coherent light can be focused to a very small spot, making it ideal for precision tasks like engraving and cutting.
The fundamental components of a laser system include the gain medium, energy source (often electrical), and an optical resonator that includes mirrors to amplify the light. Depending on the type of gain medium used, lasers can be classified into various types, such as CO₂ lasers, lasers à diodes, lasers à fibre, and UV lasers. Each type has specific characteristics that make it suitable for certain applications.
2.2 Key Components of Laser Systems
Understanding the basic components of a laser system helps in grasping the differences between Galvo and Fiber laser technologies. Here are the main components:
- Source laser: The heart of the system, generating the coherent light beam.
- Gain Medium: The material that is energized to produce laser light (par exemple., gas, semiconductor, fibre).
- Optical Resonator: Includes mirrors and lenses that amplify and focus the laser beam.
- Scanning System: In Galvo lasers, galvanometer mirrors steer the laser beam across the target material.
- Circuit de refroidissement: Essential for dissipating heat and maintaining the stability of the laser.
- Control Software: Interfaces that allow users to design, control, and monitor the engraving process.
2.3 Laser Wavelengths and Their Implications
Different lasers operate at different wavelengths, which significantly affect their interaction with various materials. Par exemple:
- Lasers UV (355nm): Known for their short wavelengths, UV lasers are capable of producing extremely fine details with minimal heat impact, making them ideal for delicate materials and high-resolution applications.
- Lasers CO₂ (10.6µm): Typically used for non-metal materials, CO₂ lasers offer smooth, clean cuts and are widely used in engraving wood, acrylique, et cuir.
- Lasers à fibre (typically around 1064nm): These are powerful and efficient, especially for metal marking and cutting. Their longer wavelengths allow for deeper penetration into materials, which is crucial for industrial applications.
- Lasers à diodes (varied wavelengths): Compact and cost-effective, diode lasers are popular for basic engraving tasks on materials like wood and plastic.
2.4 Overview of Galvo Systems
Galvo systems utilize galvanometer mirrors—small, motorized mirrors that move at high speeds to direct the laser beam. This scanning method allows for rapid and precise positioning of the laser on the target material. Galvo systems are particularly valued for:
- High-Speed Scanning: Ideal for high-volume production where speed is critical.
- Précision: Capable of achieving intricate designs with high accuracy.
- La flexibilité: Suitable for a variety of applications, especially where the workpiece is flat and the design is complex.
2.5 Overview of Fiber Laser Systems
Fiber laser systems employ optical fibers doped with rare-earth elements as the gain medium. This technology is renowned for its:
- High Power and Efficiency: Fiber lasers can deliver a concentrated beam with high power, making them excellent for metal engraving and cutting.
- Durabilité: Fiber lasers have fewer moving parts, which translates into lower maintenance and longer operational lifespans.
- Qualité du faisceau: They produce a high-quality beam that can be tightly focused, resulting in excellent detail and precision on tougher materials.
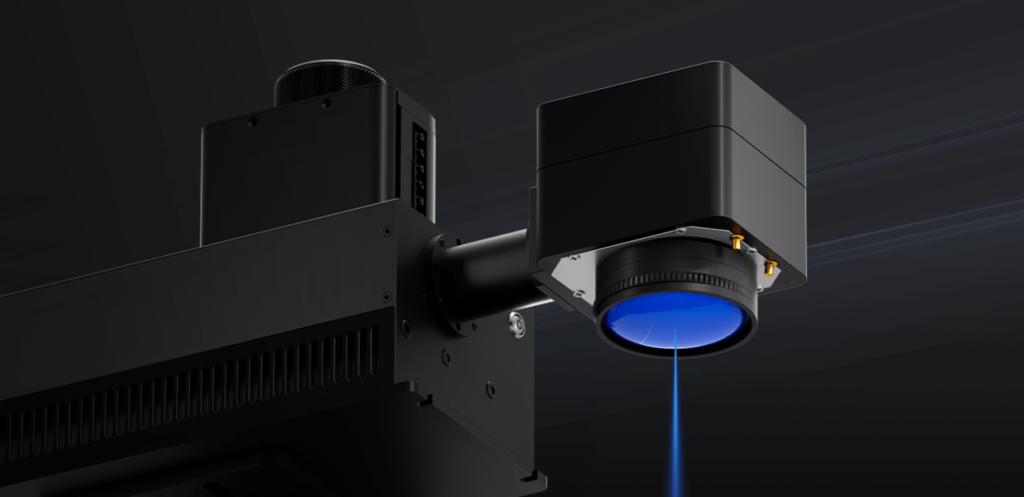
3. Deep Dive into Galvo Laser Technology
3.1 What is a Galvo Laser?
A Galvo laser system uses galvanometer mirrors to rapidly scan a laser beam across a target. These mirrors are controlled by precise electronic signals that determine the beam’s path. The speed and accuracy of the scanning system make Galvo lasers an ideal choice for applications that require detailed, high-speed marking on flat surfaces.
Galvo lasers are particularly useful for engraving intricate designs, high-speed marking, and applications where the laser beam needs to be directed dynamically across the workpiece.
3.2 Mechanics of Galvo Scanning Systems
The heart of a Galvo system lies in its galvanometer mirrors. These tiny mirrors can pivot at extremely high speeds, controlled by a servo motor. When a laser beam hits the mirror, it is deflected along a predetermined path. This rapid movement allows the laser to cover a large area in a very short time while maintaining precision.
Key aspects include:
- Scanning Speed: The ability to move the beam rapidly, which translates into faster production times.
- Positional Accuracy: Ensures that the laser hits the correct spot on the material, crucial for detailed engravings.
- Control Electronics: Advanced controllers adjust the mirror’s position in real-time, ensuring that the engraving follows the desired pattern.
3.3 Advantages of Galvo Laser Systems
Galvo laser systems have several notable advantages:
- Vitesse: They can achieve extremely high scanning speeds, making them perfect for high-volume production.
- Précision: Their accuracy allows for intricate and detailed designs, even at very high speeds.
- La flexibilité: They are suitable for a variety of applications, from small-scale artistic engravings to industrial marking.
- Rentable: For applications that do not require high power, Galvo systems are generally more affordable than fiber lasers.
3.4 The Emergence of 3D UV Galvo
The latest innovation in Galvo technology is the advent of 3D UV Galvo systèmes. These systems integrate ultraviolet (UV) laser technology with Galvo scanning to push the boundaries of precision and detail. Le 3D UV Galvo enables:
- Micron-Level Accuracy: Achieving resolutions as fine as 0.001mm for ultra-detailed work.
- 3D Engraving Capability: Extending beyond flat surface engraving to add depth and texture.
- Low Thermal Impact: The UV wavelength minimizes heat transfer, preserving the integrity of sensitive materials.
This breakthrough technology is revolutionizing industries that demand high precision in three-dimensional space, such as microelectronics, advanced labeling, and intricate art designs.
3.5 Applications of Galvo Lasers in Industry
Galvo laser systems are widely used across various industries:
- Fabrication: For high-speed marking of serial numbers, logos, and barcodes on parts and components.
- Électronique: Engraving delicate circuits and microchips with high precision.
- Emballage: Creating intricate patterns and designs on packaging materials to enhance branding.
- Art et design: Producing detailed engravings on a variety of materials for artistic projects.
- Dispositifs médicaux: Marking small, precise identifiers on medical instruments and components.
3.6 Études de cas: Galvo in Action
Étude de cas 1: Industrial Marking in Electronics
A leading electronics manufacturer integrated a Galvo laser system into their production line for engraving circuit boards. The high-speed scanning allowed for precise marking even on tiny components, reducing error rates and ensuring consistent product quality.
Étude de cas 2: Customized Art Engraving
An art studio specializing in personalized home décor used a 3D UV Galvo system to create detailed, three-dimensional engravings on glass and acrylic panels. The ability to add depth and texture revolutionized their product offerings and significantly boosted customer satisfaction.
Étude de cas 3: High-Volume Serial Numbering
In the automotive industry, a manufacturer adopted Galvo laser systems for marking serial numbers on metal parts. The high-speed and precision of the system improved traceability and quality control across the production line, reducing waste and operational costs.
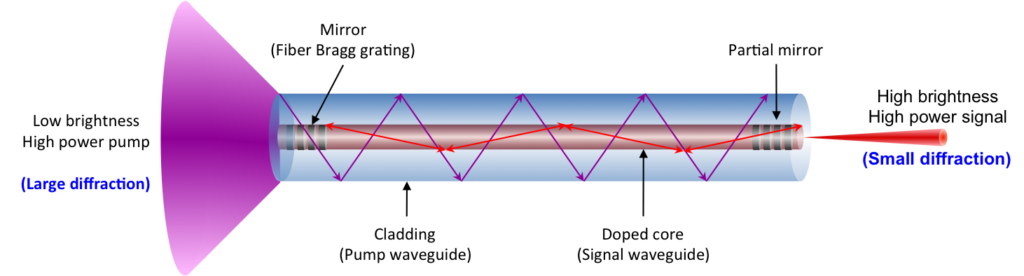
4. Deep Dive into Fiber Laser Technology
4.1 What is a Fiber Laser?
Fiber lasers use optical fibers doped with rare-earth elements as the gain medium. Unlike traditional lasers, fiber lasers are known for their exceptional power efficiency and beam quality. The design of fiber lasers minimizes moving parts, which enhances durability and reduces maintenance.
Fiber lasers are particularly renowned for:
- High Power Output: They are capable of delivering a focused, high-energy beam ideal for engraving and cutting tough materials.
- Excellent Beam Quality: The beam can be focused to a very small spot, enabling highly detailed work.
- Long Operational Lifespan: With robust construction and fewer wear-prone components, fiber lasers offer extended service life and lower maintenance costs.
4.2 Operational Principles of Fiber Lasers
Fiber lasers operate on the principle of light amplification by stimulated emission, similar to other lasers. Cependant, their unique structure allows for:
- Efficient Light Transmission: The optical fiber guides the laser light with minimal loss, resulting in a high-quality beam.
- Tight Beam Focusing: Advanced optics focus the beam to a small spot, which is essential for precision engraving.
- High Stability: The fixed fiber design reduces the risk of misalignment over time, ensuring consistent performance.
4.3 Avantages des lasers à fibre
Fiber lasers come with several advantages, notamment pour les applications industrielles:
- Puissance et vitesse: They deliver high power at rapid speeds, ideal for cutting and deep engraving.
- Versatility on Metals: Fiber lasers excel in processing metals, y compris l'acier inoxydable, aluminium, et du laiton, making them indispensable in industrial settings.
- Durabilité: With fewer mechanical components, fiber lasers have lower maintenance requirements and a longer operational life.
- Cost Efficiency in Production: Despite a higher initial investment, their long-term operating costs are often lower due to energy efficiency and reduced downtime.
4.4 Material Interaction and Performance
Fiber lasers interact with materials differently compared to Galvo systems:
- Metal Processing: Their high power makes them especially effective for engraving and cutting metals with deep, high-contrast marks.
- Non-Metals: While fiber lasers are exceptional with metals, they are less commonly used for organic materials like wood or leather, where CO₂ or diode lasers might be more suitable.
- Thermal Effects: The concentrated energy of fiber lasers can produce significant heat, which must be managed carefully to avoid damaging sensitive materials.
4.5 Applications of Fiber Lasers in Precision Processing
Fiber lasers are widely adopted in industries that require robust, grande vitesse, and precise processing capabilities:
- Automotive Manufacturing: For cutting and engraving metal parts with high precision.
- Aérospatial: Marking components with serial numbers and safety codes.
- Électronique: Engraving delicate circuits and metal casings.
- Bijoux: Creating detailed metal engravings with intricate patterns.
- Industrial Tooling: Producing custom components with high durability and precision.
4.6 Études de cas: Fiber Laser Success Stories
Étude de cas 1: High-Precision Metal Engraving
An industrial manufacturer integrated fiber laser systems for marking metal components. The precise control and high power of the fiber laser allowed for deep, permanent engravings on stainless steel parts, significantly enhancing product traceability and quality assurance.
Étude de cas 2: Custom Jewelry Production
A jewelry designer used a fiber laser to engrave intricate designs on precious metals. The exceptional beam quality of the fiber laser ensured that even the smallest details were captured flawlessly, leading to increased customer satisfaction and a premium product line.
Étude de cas 3: Aerospace Component Marking
In the aerospace sector, fiber lasers have been used to engrave critical identification marks on metal parts. The durability and precision of the fiber laser ensure that these marks remain legible and intact under extreme conditions, meeting strict regulatory standards.
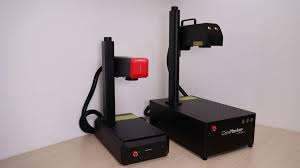
5. Comparative Analysis: Galvo vs. Laser à fibre
5.1 Performance Metrics and Specifications
When comparing Galvo and Fiber laser systems, several key performance metrics come into play:
- Vitesse: Galvo systems generally offer faster scanning speeds, making them ideal for high-volume applications on flat surfaces. Lasers à fibre, while extremely powerful, may operate at slightly slower speeds when deep engraving is required.
- Précision: Both systems are capable of high precision, but Galvo systems, especially those incorporating 3D UV Galvo technology, can achieve micron-level detail on a variety of surfaces. Lasers à fibre, d'autre part, excel in precision marking on metals.
- Power Consumption: Fiber lasers are known for their efficiency, especially in industrial applications. Galvo systems, while efficient in high-speed scanning, may consume more power depending on the application.
- Operational Lifespan: Fiber lasers typically have a longer operational lifespan with lower maintenance requirements due to fewer moving parts. Galvo systems rely on high-speed mechanical mirrors, which may require periodic maintenance.
5.2 Cost Considerations and ROI
Cost is a crucial factor when selecting a laser system:
- Investissement initial: Fiber laser systems often come with a higher initial price tag compared to Galvo systems. Cependant, their long-term durability and lower maintenance costs can result in a higher ROI over time.
- Les coûts d'exploitation: Galvo systems may have higher operational costs in high-volume applications due to increased energy usage and maintenance of moving parts. Lasers à fibre, with their efficient design, offer lower running costs, particularly in metal processing.
- Évolutivité: Consider whether your production needs may grow. Fiber lasers are generally more scalable for industrial applications, while Galvo systems are highly effective for high-speed marking and detailed engraving on flat surfaces.
5.3 Flexibility and Versatility in Application
The choice between Galvo and Fiber lasers depends largely on the range of materials you plan to process:
- Galvo Systems: Their rapid scanning capabilities make them highly versatile for non-metal materials such as wood, acrylique, et du verre. With the advent of 3D UV Galvo technology, they are now capable of complex, three-dimensional engraving.
- Lasers à fibre: These systems are best suited for metal engraving and cutting. They provide deep, high-contrast marks and are indispensable in industrial manufacturing and high-precision applications.
5.4 Maintenance and Operational Efficiency
Maintenance plays a significant role in long-term performance:
- Galvo Systems: Require regular maintenance of the mechanical scanning components. This includes cleaning and calibration of the galvanometer mirrors to maintain precision.
- Lasers à fibre: Benefit from a more robust and maintenance-free design. Their fixed optical components reduce the need for frequent adjustments, translating into higher uptime and consistent performance.
5.5 Sécurité, Reliability, and Lifespan
Safety features and device longevity are critical considerations:
- Galvo Systems: While generally safe, they require stringent safety protocols due to the high-speed movement of mirrors. Regular inspection of mechanical components is essential.
- Lasers à fibre: Known for their robust design and long lifespan. Their reduced reliance on moving parts minimizes risk and maintenance, making them a reliable choice for continuous industrial use.
5.6 Environmental Impact and Energy Efficiency
Energy consumption and environmental considerations are increasingly important:
- Galvo Systems: May consume more energy in high-speed operations but offer significant efficiency gains in high-volume, precision tasks.
- Lasers à fibre: Typically more energy-efficient due to their design and operational efficiency, making them a more sustainable option for long-term use in industrial environments.
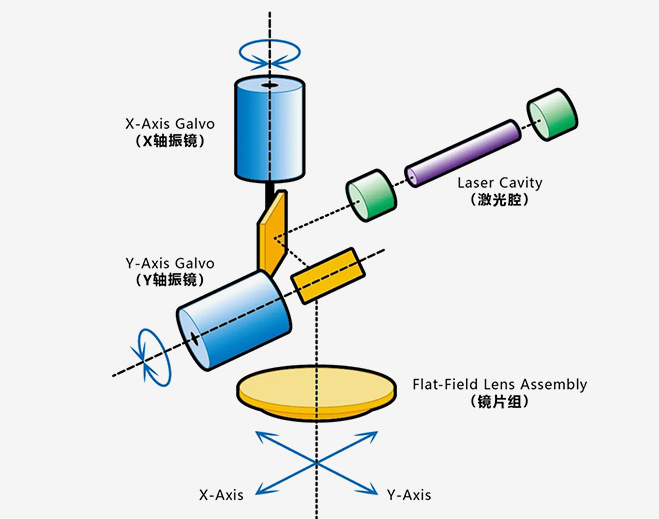
6. The Role of 3D UV Galvo in Modern Laser Systems
6.1 What is 3D UV Galvo Technology?
3D UV Galvo technology represents a significant advancement in laser processing. Combining the rapid scanning capabilities of traditional Galvo systems with the unique benefits of ultraviolet (UV) technologie laser, 3D UV Galvo systems are engineered to deliver exceptional performance in three-dimensional engraving and marking.
6.2 The Integration of 3D UV Galvo in Galvo Systems
Traditional Galvo systems primarily operate in a two-dimensional plane. Cependant, with the integration of UV laser technology, 3D UV Galvo systems extend this capability into three dimensions. This enables the system to not only mark on flat surfaces but also to create detailed, 3D engravings with variable depth and texture.
Key benefits include:
- Enhanced Detail: The UV wavelength allows for extremely fine resolution, achieving micron-level precision that is essential for high-detail work.
- Reduced Thermal Impact: UV lasers minimize heat buildup, which is critical when working with delicate or heat-sensitive materials.
- Versatile 3D Applications: From microelectronics to art, 3D UV Galvo systems open up new possibilities in design and manufacturing.
6.3 Technical Advantages of 3D UV Galvo
The integration of 3D UV Galvo technology brings several technical advantages:
- Micron-Level Precision: Achieve unparalleled detail with a resolution of up to 0.001mm.
- Dual Focal Length Flexibility: Quickly switch between fine engraving and larger area processing by adjusting the focal length.
- High-Speed Scanning: Maintain rapid processing speeds even with the additional complexity of 3D engraving.
- Low Energy Consumption: The efficient design of UV lasers helps reduce overall energy consumption while maintaining high performance.
- Extended Lifespan: Designed for industrial use, these systems are built to last, with robust components that ensure reliability over extended periods.
6.4 Applications in 3D Laser Marking and Engraving
3D UV Galvo systems are particularly well-suited for applications that require high detail and dimensional depth:
- Microelectronics: Marking and engraving on circuit boards and microchips with high precision.
- Dispositifs médicaux: Engraving FDA-compliant codes on medical equipment without inducing thermal stress.
- Applications artistiques: Creating three-dimensional textures and patterns on glass, acrylique, and other substrates.
- Marquage industriel: Producing durable, high-contrast marks on metal and other industrial materials.
6.5 Enhancing Process Precision with 3D UV Galvo
By integrating 3D UV Galvo technology, manufacturers can achieve:
- Consistent Quality: The precise control of laser parameters ensures uniform quality across high-volume production runs.
- Customizable Depth: Variable engraving depths allow for multi-level designs that add texture and dimensionality.
- Improved Accuracy: The reduction in thermal distortion and high-speed scanning capability result in exceptionally accurate markings.
6.6 Future Developments in 3D UV Galvo
Looking ahead, the potential for 3D UV Galvo technology is vast:
- Enhanced Automation: Future models may integrate AI and machine learning for real-time adjustments and improved accuracy.
- Compatibilité matérielle plus large: Ongoing research could extend the range of materials that 3D UV Galvo systems can process.
- Integration with Smart Manufacturing: As Industry 4.0 evolves, these systems will likely become more connected, enabling remote monitoring, predictive maintenance, and seamless integration into automated production lines.
7. Practical Considerations for Selecting the Right Laser System
7.1 Evaluating Your Production Needs
Before deciding between a Galvo or Fiber laser system, assess your production requirements:
- Volume: Consider the quantity of items you need to produce. High-volume operations might benefit from the speed of Galvo systems, while precision metal marking may require a fiber laser.
- Matériel: Identify the primary materials you will work with. For non-metal applications, a Galvo system with 3D UV capability may be ideal, whereas fiber lasers excel with metals.
- Complexité: Evaluate the complexity of the designs you intend to produce. High-detail, intricate designs may necessitate the fine control provided by 3D UV Galvo systems.
7.2 Material Compatibility and Processing Capabilities
Select a system that can handle the range of materials you plan to work with:
- Non-Metals: Bois, acrylique, cuir, and glass are best handled by Galvo systems with UV lasers.
- Les métaux: For high-precision metal engraving and cutting, fiber lasers are typically more effective.
- Multi-Material Processing: If you require versatility, consider a hybrid solution or a system that offers upgrade options.
7.3 Workspace and Infrastructure Requirements
Consider the physical space and environmental conditions of your workspace:
- Size and Footprint: Desktop laser systems are ideal for small workshops, while larger industrial systems may require dedicated space.
- Ventilation et refroidissement: Ensure that your workspace can support proper ventilation and temperature control, as high-power lasers generate significant heat.
- Power Supply: Verify that your facility’s electrical infrastructure meets the requirements of the chosen laser system.
7.4 Software and Control System Integration
A user-friendly control system is essential for smooth operation:
- Compatibilité logicielle: Ensure that the laser system supports popular design software like LightBurn, CorelDRAW, Adobe Illustrator, or EZCad.
- Interface utilisateur: Look for intuitive interfaces that reduce the learning curve and allow for easy adjustments.
- Connectivity: Options such as USB, Wi-Fi, or Bluetooth can enhance operational flexibility.
7.5 Scalability and Future-Proofing Your Investment
Plan for future growth:
- Conception modulaire: Choose systems with modular components that can be upgraded or replaced as technology evolves.
- Integration Capabilities: Consider systems that can be integrated into larger automated production lines or smart manufacturing systems.
- Manufacturer Support: Long-term support, firmware updates, and customer service are crucial for maintaining system performance.
7.6 Service client, garantie, and After-Sales Service
Reliable after-sales service can significantly impact your overall experience:
- Warranty Coverage: Review warranty terms to ensure long-term protection for your investment.
- Soutien technique: Check if the manufacturer offers 24/7 technical support, online resources, and on-site training.
- Maintenance Programs: Look for maintenance programs that offer regular servicing, updates, and spare parts availability.
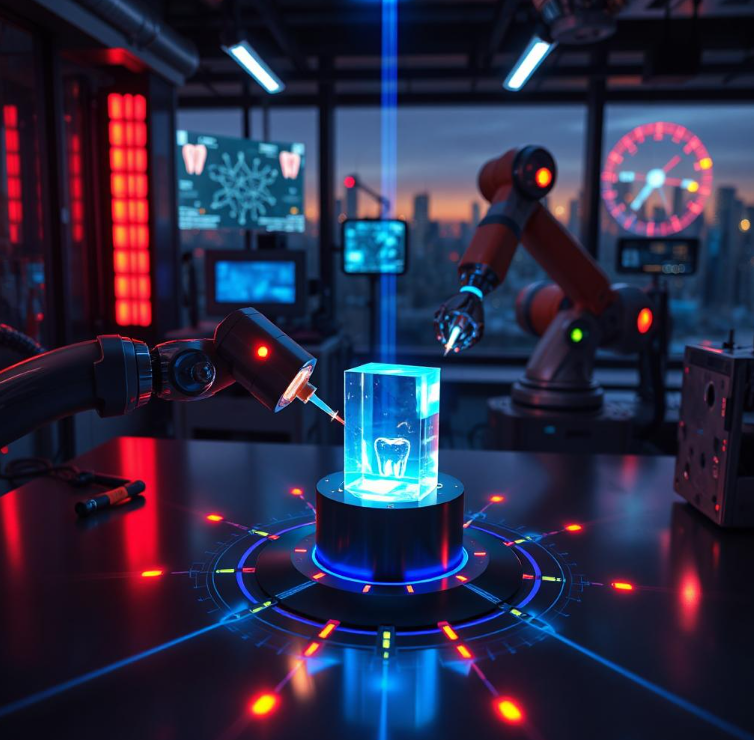
8. Future Trends and Innovations in Laser Technology
8.1 The Impact of Smart Manufacturing and Industry 4.0
The convergence of laser technology with smart manufacturing and Industry 4.0 is reshaping production:
- Automatisation: Increased automation reduces manual intervention, enhancing consistency and productivity.
- Data-Driven Processes: Integration with IoT devices enables real-time monitoring and predictive maintenance.
- Remote Control and Monitoring: Advances in connectivity allow for remote operation and troubleshooting, reducing downtime.
8.2 Innovations in Laser Cooling and Energy Management
Energy efficiency and cooling are critical areas of innovation:
- Advanced Cooling Systems: New designs incorporate both water and air cooling for optimal thermal management.
- Reduced Energy Consumption: Improved laser efficiency translates to lower operating costs and reduced environmental impact.
- Sustainable Production: As environmental regulations tighten, energy-efficient laser systems will be favored in green manufacturing initiatives.
8.3 Advances in Automation and Remote Monitoring
The future of laser processing lies in smarter, more connected systems:
- Automated Calibration: AI-driven calibration systems can adjust laser parameters in real time.
- Remote Diagnostics: Cloud-based monitoring tools allow operators to diagnose issues and optimize performance remotely.
- Integrated Workflow Solutions: Seamless integration with design software and production management systems will streamline operations.
8.4 Emerging Applications in Healthcare, Électronique, and Beyond
Laser technology continues to expand into new industries:
- Healthcare: High-precision lasers are used for medical device marking, outils chirurgicaux, and even direct medical applications.
- Électronique: Enhanced precision is crucial for marking PCB boards and microelectronic components.
- Advanced Materials: Emerging materials and composite structures require laser systems with specialized capabilities.
8.5 The Convergence of AI and Laser Processing Technologies
Artificial Intelligence (IA) is set to transform laser processing:
- Predictive Maintenance: AI algorithms can predict component failures before they occur, reducing downtime.
- Enhanced Process Control: Machine learning models can optimize laser settings based on material properties and design complexity.
- Personnalisation et personnalisation: AI-driven design tools will enable more personalized production runs, catering to individual customer preferences.
8.6 Market Forecasts and Industry Predictions for 2025 and Beyond
The laser processing market is poised for significant growth:
- Adoption accrue: More small and medium-sized enterprises are expected to adopt laser engraving technology.
- Technological Maturation: Advances in laser technology will drive down costs and improve accessibility.
- Global Trends: Emerging markets and increasing demand for customization will fuel growth in the laser processing industry.
9. Foire aux questions (FAQ)
T1: What are the primary differences between Galvo and Fiber Lasers?
UN: Galvo systems utilize high-speed scanning mirrors to direct the laser beam across a flat surface, ideal for high-speed marking on non-metal materials. Lasers à fibre, d'autre part, offer high power and precision for metal engraving and cutting, with fewer moving parts and greater durability. Each system has its unique strengths depending on your material and application needs.
T2: How does 3D UV Galvo technology improve laser performance?
UN: 3D UV Galvo technology integrates ultraviolet laser capabilities with rapid scanning to achieve micron-level precision and three-dimensional engraving. This technology minimizes thermal impact and allows for intricate, multi-depth designs on various materials, enhancing both quality and versatility.
T3: Which laser system is best for high-precision metal marking?
UN: For high-precision metal marking, fiber lasers are generally preferred due to their high power and tight beam focus. Cependant, for non-metal applications requiring intricate details, a Galvo system—especially one incorporating 3D UV Galvo technology—can deliver exceptional results.
T4: Can fiber lasers engrave non-metal materials effectively?
UN: While fiber lasers excel in metal processing, they are not typically the first choice for non-metal materials. For materials like wood, acrylique, et cuir, CO₂ or diode lasers are more commonly used. Each laser type is optimized for different material interactions.
Q5: What are the maintenance requirements for Galvo and Fiber Laser systems?
UN: Galvo systems require regular cleaning and calibration of the scanning mirrors and optics, while fiber lasers, with their robust design, typically demand less frequent maintenance. Regular inspections, cleaning, and software updates are essential for both systems to ensure optimal performance.
Q6: How do cost and ROI compare between Galvo and Fiber Laser technologies?
UN: While fiber lasers often come with a higher upfront cost, their longevity, efficacité, and lower maintenance costs can lead to a better ROI in high-volume, applications industrielles. Galvo systems are typically more cost-effective for high-speed marking on non-metal materials and offer excellent precision for detailed work.
Q7: What safety measures should be taken when operating these systems?
UN: Always use proper laser safety goggles, ensure adequate ventilation, and follow manufacturer guidelines. Both Galvo and fiber laser systems have built-in safety features, such as automatic shut-off mechanisms and interlocks, to minimize risk during operation.
Dernières pensées
The laser processing landscape is evolving rapidly, and as we move further into 2025, the choice between Galvo and Fiber laser systems becomes more critical than ever. With innovations like 3D UV Galvo leading the charge, businesses have an unprecedented opportunity to achieve extraordinary levels of precision, efficacité, and creativity. By understanding the core differences, avantages, and applications of each system, you are now better equipped to select the laser engraving solution that best meets your needs.
Step into the future of laser technology and unlock the full potential of your production processes. Whether you choose a Galvo system with cutting-edge 3D UV capabilities or a high-powered fiber laser for metal processing, the future is bright—and the possibilities are endless.