To prepare a photo for laser engraving, you need to follow several detailed steps to ensure optimal results. Let’s break down the process into a clear, step-by-step guide, addressing common challenges and best practices:
Step 1: Choosing the Right Photo
Selecting the correct photo is critical to achieve a high-quality laser engraving. Here’s what you need to consider:
- High Contrast: Photos with a strong contrast between light and dark areas are ideal. The laser engraver works by burning or marking material, and sharp transitions in tone allow for a more detailed result.
- Simplicity: Avoid highly complex images with intricate backgrounds or too much fine detail. The laser struggles to engrave subtle gradients or intricate elements, which can result in a blurry or washed-out image.
- Resolution: Choose images with a high resolution (at least 300 DPI) to avoid pixelation during the engraving process. Low-resolution images may look fine on a screen but will degrade when resized or processed for engraving.
Common Challenges:
- Low-light photos may lose important details when processed for engraving.
- Overly busy backgrounds can make the primary subject difficult to distinguish.
- Excessive detail can overwhelm the laser engraver, reducing clarity.
Step 2: Preparing the Photo in Editing Software
Before engraving, you’ll need to use image editing software like Adobe Photoshop, GIMP, or CorelDRAW to optimize the photo. Here are the steps to follow:
1. Convert to Grayscale
Laser engravers usually work in grayscale, interpreting different shades of gray as varying degrees of engraving depth or burn intensity. Converting your photo to black and white allows you to see exactly how the laser will interpret the image.
- Method:
- In Photoshop:
Image > Mode > Grayscale
. - In GIMP:
Colors > Desaturate
.
- In Photoshop:
By converting to grayscale early in the process, you can fine-tune the image before the engraving.
Common Challenges:
- Loss of Detail: Some fine details may get lost when converting to grayscale, especially in images with soft shadows or complex textures.
- Flat Images: Grayscale images might appear flat; adjust the contrast to enhance the important areas.
2. Adjust Brightness & Contrast
To further enhance the image, adjust the brightness and contrast. Boosting contrast will exaggerate the difference between light and dark areas, making the engraving more defined.
- Method:
- In Photoshop:
Image > Adjustments > Brightness/Contrast
.
- In Photoshop:
A typical adjustment might involve increasing the contrast by 20–50%, depending on the image. Be careful not to increase it too much, as you might lose midtones (the transition between light and dark).
Common Challenges:
- Overexposure: Increasing contrast excessively can result in the loss of important midtones, leaving the engraving with overly harsh transitions.
3. Sharpen the Image
For best engraving results, apply a sharpening filter to make edges more defined.
- Method:
- In Photoshop:
Filter > Sharpen > Unsharp Mask
.
- In Photoshop:
Use the Unsharp Mask to control the intensity and radius of the sharpening. This makes the details stand out more when engraved, particularly if the original image was slightly blurry or soft.
Common Challenges:
- Excessive Sharpening: Over-sharpening can introduce artifacts or noise into the image, which may appear as unwanted marks in the final engraving.
4. Resize & Crop
Make sure the image fits the size of the material you’re engraving on. Resize the image according to the workspace of your laser engraver. It’s also a good time to crop unnecessary elements that don’t add value to the final product.
- Method:
- In Photoshop:
Image > Image Size
orImage > Canvas Size
.
- In Photoshop:
You can also crop out unnecessary parts using the Crop tool. Make sure to maintain the aspect ratio to prevent the image from becoming distorted.
Common Challenges:
- Image Distortion: Resizing an image without maintaining its aspect ratio can lead to distorted or stretched engravings.
Step 3: Convert the Image to Bitmap
Once your image is ready, convert it into a bitmap format, which helps the laser interpret the image as a series of dots rather than continuous tones. This step is critical for ensuring that the photo engraves well on various materials.
- Method:
- In Photoshop:
Image > Mode > Bitmap
.
- In Photoshop:
You can choose different bitmap conversion methods, such as halftone or diffusion dither. These methods determine how the laser interprets the shades of gray in the image.
Common Challenges:
- Choosing the Wrong Method: The wrong bitmap conversion method can result in a poorly defined engraving. Experiment with different options to find what works best for your specific image and material.
Step 4: Prepare the Laser Engraver Settings
Next, you need to configure the settings on your laser engraver. Settings vary depending on the material you’re working with (wood, metal, acrylic, etc.) and the type of engraver you’re using (CO2, fiber, etc.).
1. Power & Speed Settings
Adjust the power and speed settings based on your material and the depth of engraving you want. For photos, you’ll typically want a lighter engraving, so lower power settings and faster speeds are usually better.
- Wood: Low to medium power, medium speed.
- Metal: Higher power, slower speed.
2. DPI Setting
Set the DPI (dots per inch) on the laser engraver, usually matching the resolution of your image. 300 DPI is a good starting point for most photo engravings.
Common Challenges:
- Incorrect Power Settings: Too much power can burn through delicate materials like wood or acrylic, while too little power might not engrave deep enough.
- Low DPI Settings: Using a low DPI can result in a rough, pixelated engraving, particularly in detailed images.
Step 5: Performing a Test Engraving
Before engraving your photo on the final material, always perform a test on scrap material. This lets you adjust settings without wasting expensive materials.
- Check for clarity, depth, and contrast during your test run.
- Adjust power, speed, and focus based on your test results.
Common Challenges:
- Material Mismatch: The final material might engrave differently than your test material, so always use a similar material for testing.
Step 6: Mirroring the Image (Optional)
If engraving on glass or transparent materials, you may need to mirror the image so it appears correctly when viewed from the other side.
- Method:
- In Photoshop:
Image > Image Rotation > Flip Canvas Horizontal
.
- In Photoshop:
Common Challenges:
- Forgetting to Mirror: Engraving directly onto transparent surfaces without mirroring will result in a reversed image when viewed from the front.
Step 7: Final Engraving
After all adjustments, send the image to the laser engraver for the final engraving. Monitor the engraving process to ensure everything runs smoothly and make any last-minute adjustments if needed.
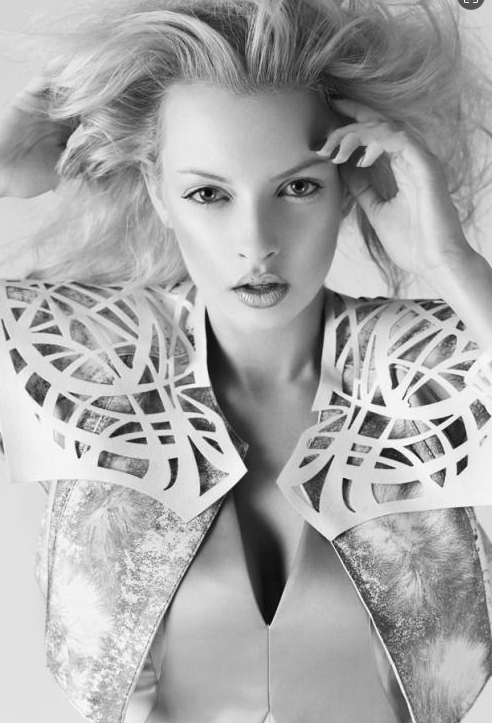
Frequently Encountered Issues and Solutions
- Blurry Engravings: This could be due to the image resolution or improper focus. Always use a high-resolution image (300 DPI) and double-check the focus of your laser engraver.
- Uneven Engraving Depth: If the engraving appears deeper in some areas than others, the laser’s power or speed settings may need adjusting. Uneven surfaces can also cause this issue.
- Overburning: Too much laser power can cause excessive burning, particularly on wood or acrylic. Lower the power and run tests to find the sweet spot for your material.
- Loss of Detail in Fine Areas: If small details are being lost, try increasing the contrast during the image editing stage or sharpening the edges in your editing software.
- Ghosting or Double Lines: This is usually caused by the laser beam reflecting off the material or multiple passes with slight misalignment. You may need to adjust the laser’s focus or recalibrate the engraving bed.
By following these detailed steps, you can successfully prepare any photo for laser engraving, ensuring high-quality results.