Understanding Laser Engraving on Aluminum
Laser engraving has become an essential tool in the precision manufacturing industry, especially when it comes to creating intricate designs on materials like aluminum. Whether you are creating custom jewelry, industrial parts, or promotional products, understanding how to engrave aluminum with a laser is crucial for achieving high-quality results. This article will delve into the specifics of laser engraving material aluminum, including its properties, the laser engraving process, the types of lasers to use, and tips for successful engraving.
What is Laser Engraving on Aluminum?
Laser engraving on aluminum involves using a high-powered laser to etch or mark the surface of the material, creating designs, logos, text, or patterns. The process uses a focused beam of light to remove or alter the surface layer, leaving a permanent, precise mark. Aluminum is a popular choice for engraving due to its lightweight, durable, and corrosion-resistant properties, making it ideal for various applications.
Why Aluminum?
Aluminum is widely used in industries such as aerospace, automotive, and consumer goods due to its strength-to-weight ratio, conductivity, and resistance to corrosion. The versatility of aluminum makes it a prime candidate for laser engraving, offering clean and sharp engravings that last for years.
Laser Engraving on Aluminum: Why Choose It?
Laser engraving on aluminum offers several advantages:
- Precision: Laser engraving provides micron-level accuracy, making it ideal for intricate designs, fine details, and small text.
- Durability: Laser-engraved marks on aluminum are permanent and resistant to wear and tear, making it a great option for high-use or high-abrasion applications.
- Flexibility: Laser engraving allows for customization of designs on a wide range of aluminum products, including anodized and raw aluminum.
- Speed: Laser engraving is fast, allowing for efficient production and quick turnarounds on projects.
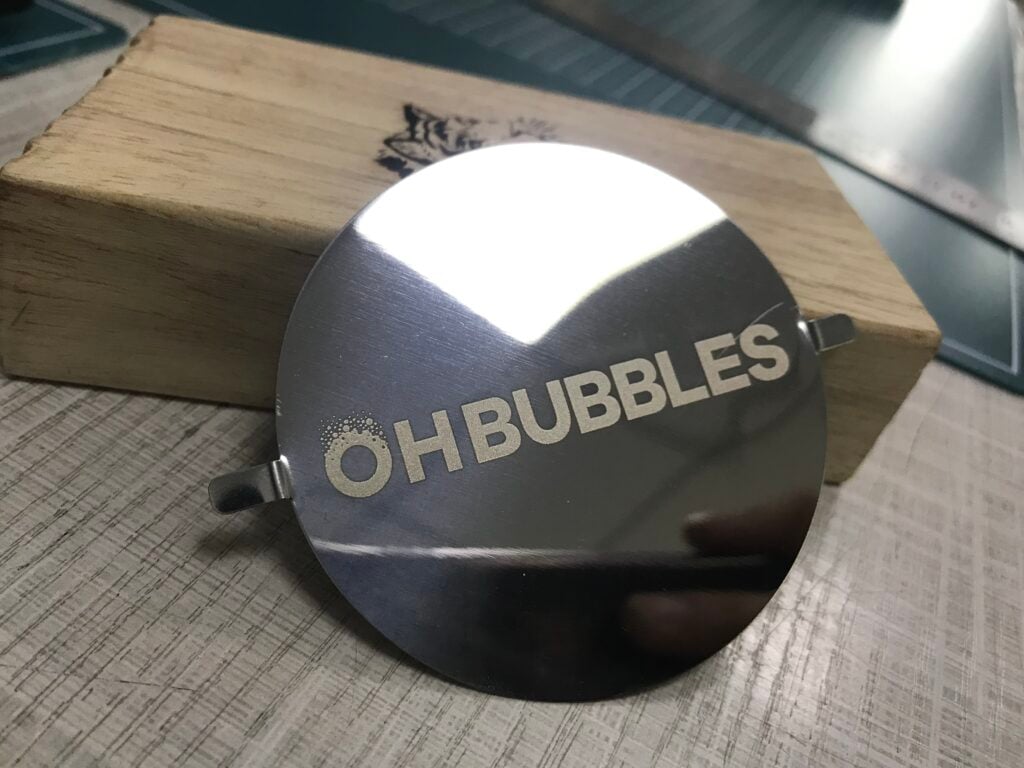
How Does Laser Engraving Work on Aluminum?
Laser engraving works by directing a focused beam of light onto the aluminum’s surface. The laser’s high energy vaporizes or melts the material, creating a permanent mark. Depending on the power settings, speed, and frequency, the laser can either produce shallow engravings (for decorative designs) or deeper engravings (for markings like serial numbers).
Key Laser Types for Engraving Aluminum:
The two primary types of lasers used for engraving aluminum are CO2 lasers and fiber lasers. Each has unique capabilities and applications.
- CO2 Lasers: Ideal for engraving anodized aluminum or aluminum that has been coated or treated. They operate at a wavelength of 10.6 µm, which is absorbed by the coating and used to etch surface designs. However, CO2 lasers are less effective on raw, reflective aluminum.
- Fiber Lasers: Fiber lasers operate at a much shorter wavelength (typically 1.06 µm) and are more effective at engraving raw, untreated aluminum. These lasers can create deep, high-contrast engravings and are ideal for precise markings on industrial parts.
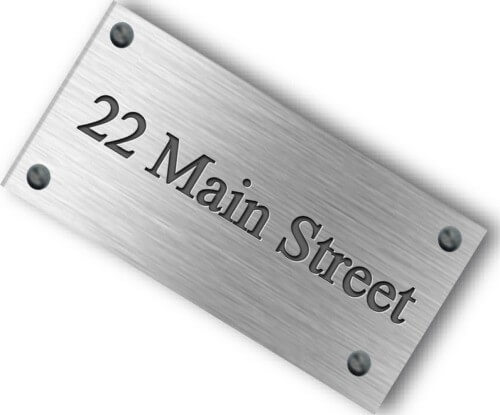
Factors Affecting Laser Engraving on Aluminum:
Several factors play a role in achieving the best results when engraving aluminum:
- Laser Power: The power setting determines how deep the engraving goes. For raw aluminum, higher power settings (20W to 50W for fiber lasers) are often required for deeper marks. Lower power settings (10W to 20W) are ideal for finer details and surface markings.
- Speed: Engraving speed affects the intensity of the mark. Slower speeds allow for deeper engravings, while faster speeds are better suited for surface-level markings and faster production times.
- Frequency: Laser frequency refers to the number of laser pulses per second. Higher frequency settings are ideal for creating smoother, more polished engravings, while lower frequency settings may give a more textured or frosted appearance.
- Focus: Correctly focusing the laser is essential for achieving precision. A properly focused laser produces cleaner, sharper engravings, while an unfocused laser may result in blurry or inconsistent marks.
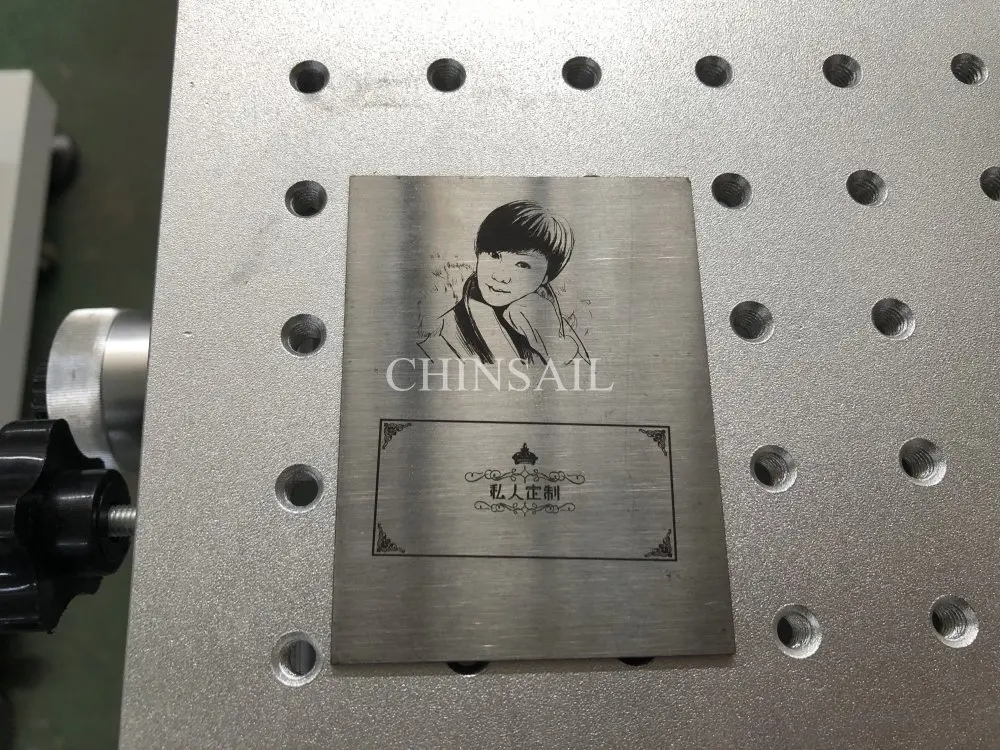
Types of Aluminum Suitable for Laser Engraving:
Aluminum comes in several forms, and different types may require slightly different engraving techniques.
- Anodized Aluminum: Anodized aluminum has a protective oxide layer that makes it more resistant to corrosion. It is one of the best materials for laser engraving because it provides excellent contrast and does not require additional treatments.
- Raw Aluminum: Raw, untreated aluminum can be engraved with fiber lasers but may produce lighter marks. For deeper engraving on raw aluminum, higher laser power and slow engraving speeds are required.
- Aluminum Composites: These materials, which combine aluminum with other materials like plastics or ceramics, can be challenging to engrave but can yield interesting results when done correctly.
Applications of Laser Engraving on Aluminum:
Laser engraving on aluminum has widespread applications across many industries:
- Industrial Marking: Laser engraving is commonly used for marking parts with serial numbers, barcodes, or other identifying information. The precision of laser engraving ensures that these marks are clear, legible, and permanent.
- Custom Jewelry: Aluminum is increasingly being used in jewelry, especially anodized aluminum, which can be engraved with intricate designs, logos, and names for personalization.
- Promotional Products: Laser engraving is ideal for creating custom promotional items like keychains, mugs, and pens. Aluminum’s durability ensures that the engravings last over time, even with frequent use.
- Aerospace and Automotive: Aluminum parts in the aerospace and automotive industries often require engraving for identification, calibration markings, and traceability.
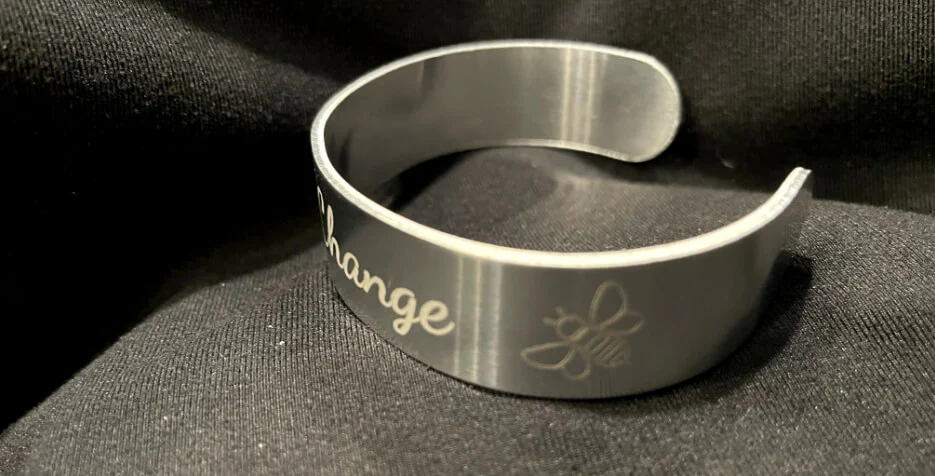
Best Practices for Laser Engraving on Aluminum:
To achieve the best results, follow these tips:
- Test Before Engraving: Always conduct test engravings on scrap pieces of aluminum to fine-tune your settings and ensure optimal results.
- Use the Right Lens: Use a lens with the correct focal length for engraving aluminum. This ensures the laser remains focused and delivers clean, precise engravings.
- Maintain Laser Focus: Ensure that the laser remains focused throughout the engraving process. Unfocused lasers can cause distortion and loss of detail.
- Use Air Assist: Air assist is a helpful feature for laser engraving on metals. It helps remove debris from the engraving surface, reduces the heat build-up, and prevents discoloration.
- Proper Cooling: Lasers generate heat during engraving, and aluminum, being a good heat conductor, requires efficient cooling to maintain consistent performance and prevent damage to the material.
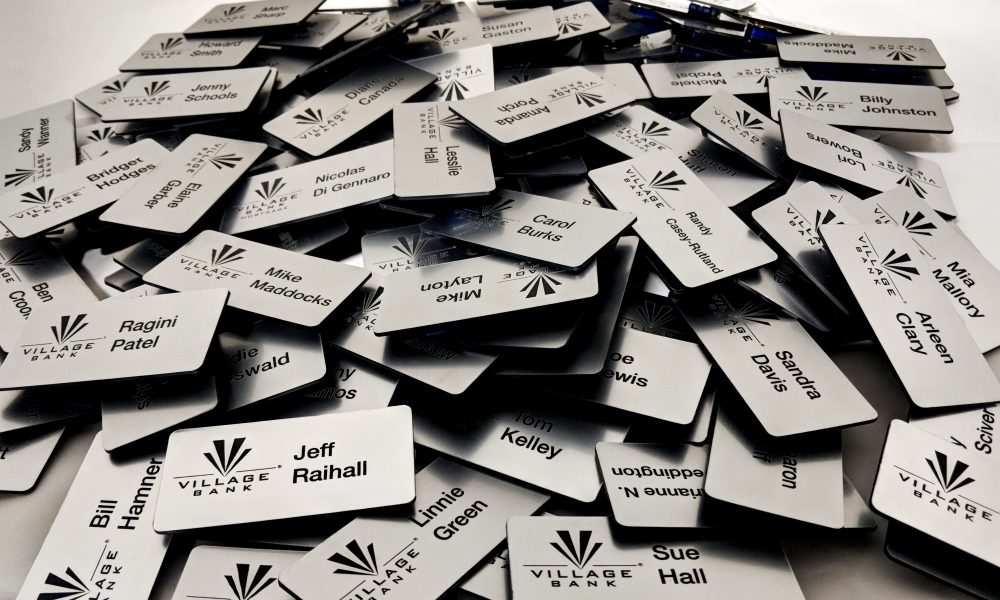
Challenges in Laser Engraving Aluminum:
While laser engraving aluminum is highly effective, there are some challenges to consider:
- Reflectivity of Raw Aluminum: Raw aluminum can be highly reflective, which can cause issues with certain types of lasers, especially CO2 lasers. Using a fiber laser or anodized aluminum helps mitigate this issue.
- Heat Build-Up: Excessive heat build-up during the engraving process can cause warping or deformation of aluminum. Using air assist and fine-tuning the settings can help manage heat distribution.
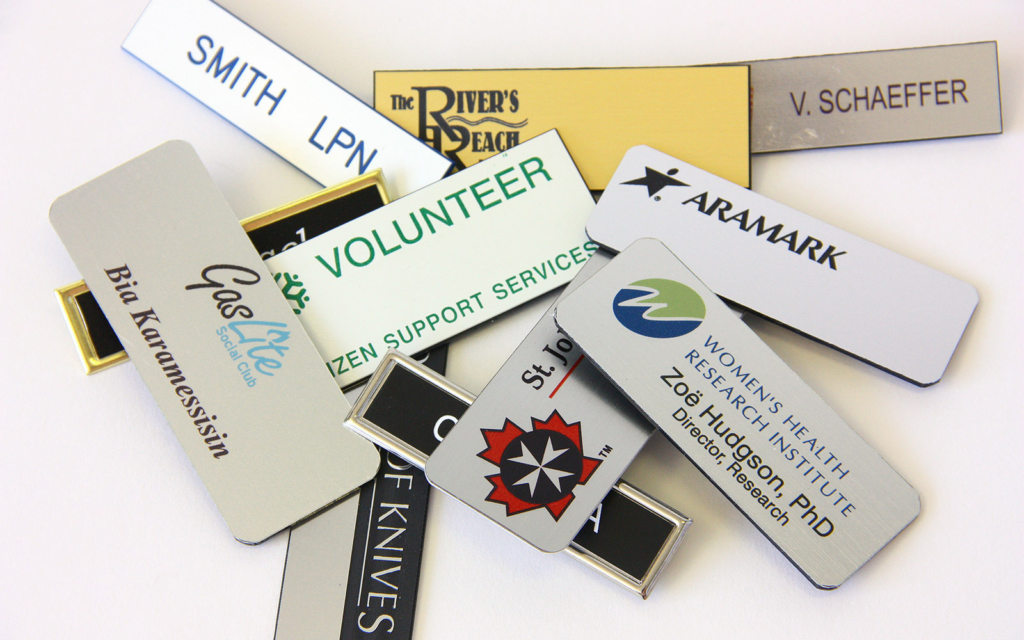
Laser Engraving on Aluminum: Troubleshooting Tips
If you’re experiencing issues with your laser engravings on aluminum, here are some troubleshooting tips:
- Faint or Inconsistent Engraving: Check your laser power and speed settings. Increase the power for deeper engravings, or decrease the speed for finer details.
- Burnt or Damaged Aluminum: If the surface appears burnt, reduce the power and increase the speed to minimize excessive heat.
- Poor Contrast: If the engraving is not showing up well, consider switching to anodized aluminum for better contrast.
Mastering Laser Engraving on Aluminum
Laser engraving on aluminum offers incredible potential for professionals across various industries. Whether you’re working with raw aluminum or anodized aluminum, the precision, durability, and speed provided by lasers ensure high-quality results every time. By understanding the material properties, choosing the right laser, and optimizing your settings, you can achieve flawless engravings on aluminum that stand the test of time.
Laser engraving has become an invaluable tool in modern manufacturing and personalization. If you’re working with aluminum, mastering the techniques outlined in this guide will help you take your engraving skills to the next level. Whether you’re engraving industrial parts, creating personalized jewelry, or crafting custom promotional items, laser engraving offers endless possibilities.