In today’s workshop, the focus is on introducing a cutting-edge technology: the fiber laser, particularly the commarker B4 20-watt fiber laser. The presenter, having received this equipment for evaluation, expressed enthusiasm about exploring its capabilities, noting it as their first encounter with this type of laser technology.
Before delving into the specifics, a disclaimer was made acknowledging the presenter’s limited experience with fiber and Galvo laser engraver. They humbly requested the viewers’ understanding, inviting input and guidance from those more seasoned in this field.
Describing the commarker B4 20-watt fiber laser engraving machine, the presenter elucidated its galvo operation, powered by a galvanometer system directing the laser beam onto the work surface. They highlighted the laser’s precision, attributed to its fast-moving mirrors and a lens that focuses the beam to a pinpoint accuracy. However, it was noted that this precision came at the cost of a reduced working area.
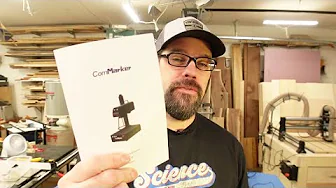
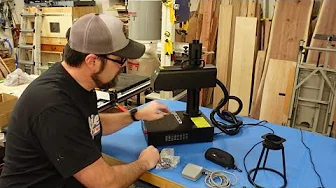
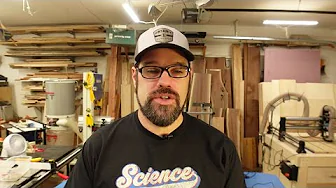
The laser’s technical specifications were then detailed, including its infrared wavelength, frequency range, spot size, and engraving speed. While the laser boasted impressive capabilities for working with metals and synthetics, its effectiveness on natural and clear materials was acknowledged to be limited.
In addition to its core functionalities, the presenter discussed the software compatibility and accessory features of the laser, such as the foot pedal for repeated markings and the detachable head for engraving larger objects.
Lens option-
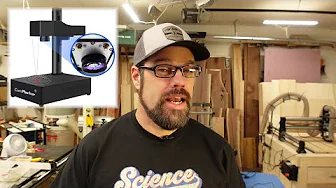
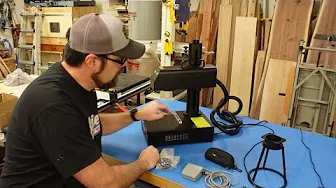
The lens options offered with the commarker B4 20-watt fiber laser engraver provide users with versatility in their work. Two lens options are available: a 110 by 110mm lens and a 200 by 200mm lens. It’s important to note the trade-offs between the two options. While the 200mm lens widens the work area, it also enlarges the spot size of the laser beam. Consequently, users may sacrifice some detail in exchange for the ability to work on larger areas at potentially higher speeds. This decision, therefore, depends on the specific requirements of the task at hand – whether prioritizing speed and coverage or intricacy and precision.
Software-
Moreover, the laser comes equipped with EZCAD 2 software out of the box, offering comprehensive features for operation. However, for users accustomed to Lightburn software, there is the option to upgrade their license to support the Galvo style laser through EZCAD 2. This compatibility ensures a seamless transition for users, allowing them to work with their existing files without hassle.
The efficiency and safety of laser equipment are crucial factors to consider, especially when they are shipped and assembled. In this regard, the laser under discussion demonstrates commendable packaging and assembly features, contributing to a smooth user experience and safeguarding against potential hazards.
Packing –
Firstly, the laser arrives meticulously packed in a double box, fortified with Kaizen-type foam for optimal insulation. This packaging not only ensures the protection of delicate components during transit but also signifies a commitment to quality by the manufacturer. Despite encountering minor damage to the shipping box, the robust packing methodology mitigates any consequential harm to the contents, affirming its effectiveness.
Assembly of the laser is straightforward, facilitated by comprehensive instructions and supplementary resources. The accompanying manual, supplemented with illustrative photographs, serves as a practical guide for users, while additional instructional videos on the SD card or accessible via the manufacturer’s YouTube channel further enhance the assembly process. The step-by-step procedure involves attaching various components such as the Tower, coupling, focus coupling rod, and handle, culminating in a fully assembled unit ready for operation.
Upon assembly, the laser’s exterior design manifests as an integrated unit, housing essential electronics, power supply, and fiber source within a cohesive structure. Furthermore, provisions for customization and adaptability are evident, with features such as detachable components and threaded holes for personalized jig setups, facilitating precision and repeatability in cutting applications.
Safety Protective-
However, attention to safety remains paramount, particularly concerning the use of protective eyewear and adherence to safety protocols. While the provided glasses offer a degree of protection, the absence of detailed specifications regarding their optical properties raises concerns regarding their efficacy. Clear documentation specifying wavelength and optical density would instill greater confidence in their protective capabilities, especially given the potential risks associated with laser exposure. Moreover, the inclusion of safety features such as an emergency stop button underscores a commitment to user safety, providing a failsafe mechanism to halt operations in the event of unforeseen mishaps. Additionally, proactive measures to mitigate airborne particulate emissions, such as utilizing enclosures or filtration systems, are imperative to safeguarding both equipment integrity and operator health.
The laser’s commendable packaging, user-friendly assembly process, and emphasis on safety underscore its suitability for various applications. However, continued efforts to enhance safety documentation and implement proactive measures against airborne particulates are essential to further elevate user confidence and operational efficiency.
Appearance-
Examining the rear panel of the laser, it is evident that meticulous attention has been paid to the provision of essential connectivity options. The umbilical cord facilitates the transmission of power and fiber laser source signals to the head unit, ensuring seamless operation. Additionally, standard ports such as the PC port power cable and USB interface are conveniently located, catering to diverse user requirements.
Furthermore, the inclusion of a USB A to B cable, accompanied by USB A to C adapters, demonstrates a thoughtful approach toward user convenience and compatibility. This provision ensures that users with newer laptops devoid of traditional USB A connectors can seamlessly integrate the laser into their workflow without encountering compatibility issues.
Moreover, the presence of barrel connectors on the rear panel serves to enhance operational versatility. These connectors facilitate the integration of peripheral devices such as foot pedals and rotary adapters, enabling precise control and customization as per user preferences.
Moving to the front panel, the intuitive layout of buttons underscores the user-centric design philosophy adopted by the manufacturer. The dedicated power button, coupled with arrow keys for adjusting focus, empowers users with effortless control over laser operations. Additionally, the inclusion of Red Dot framing functionality, denoted by the ‘R’ and ‘M’ buttons, further enhances precision and accuracy during engraving tasks.
Furthermore, the provision of a hand crank for manual focus adjustment offers users an alternative method for achieving optimal focus, complementing the electronic controls available on the base unit. This feature not only affords users finer control but also ensures consistent and reliable results across various applications.
ComMarker B4 laser engraver meticulous design and thoughtful integration of connectivity options and control features on the laser unit underscore its suitability for diverse applications. The seamless combination of functionality and user convenience exemplifies a commitment to delivering a superior user experience.
BUSINESS CARD TESTING –
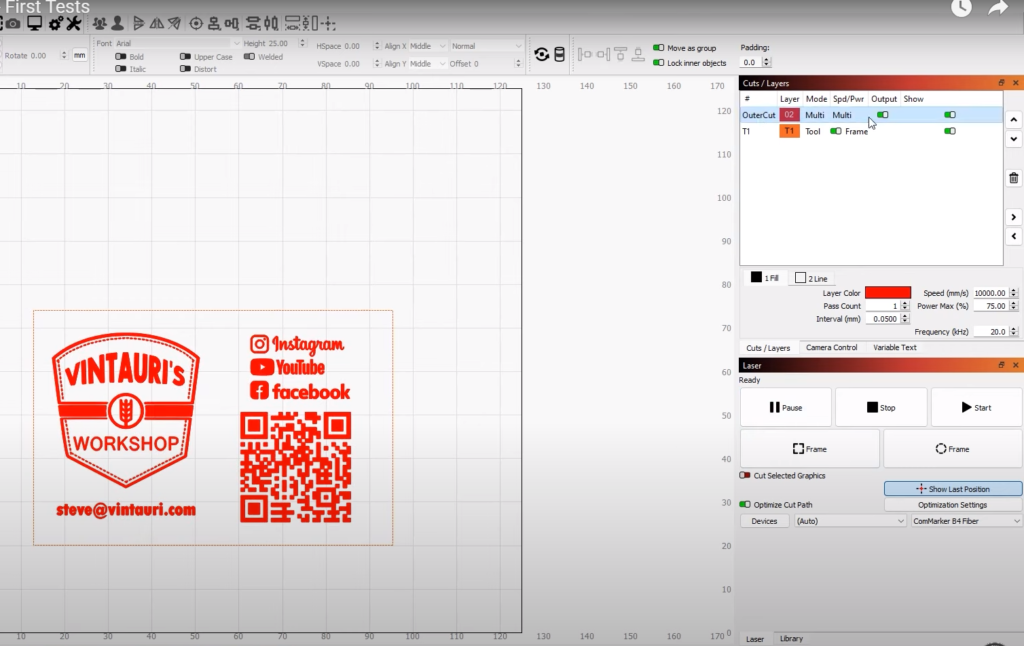
In the process of engraving business cards, a meticulous approach is taken to ensure precision and efficiency. The individual, equipped with the necessary alignment tools and utilizing the LightBurn software, meticulously sets up a simple business card file. This file incorporates essential elements such as logos, contact information, and QR codes, strategically placed to enhance brand visibility and engagement.
Through LightBurn’s intuitive interface, the individual navigates through various layers and settings to optimize the engraving process. Fine-tuning parameters such as scan angles, line intervals, and power levels ensure optimal results, particularly when working with anodized aluminum cards. The use of cross-hatch patterns and multi-pass configurations further enhances the quality of the engraving, minimizing imperfections and ensuring a solid fill.
Upon finalizing the settings, the individual initiates the engraving process through LightBurn, leveraging its convenient features such as real-time previews and adjustments. The seamless execution of the engraving job results in a professionally finished business card in less than a minute, showcasing the efficiency and effectiveness of the chosen workflow.
Furthermore, the integration of external peripherals, such as foot pedals, into the engraving process demonstrates a commitment to optimizing workflow efficiency. By configuring LightBurn settings to accommodate foot pedal control, the individual enables seamless execution of repeated cuts without the need for constant computer intervention.
In the pursuit of exploring the potential of laser engraology, a series of material tests were conducted. The focus of one such test was to ascertain the feasibility of inducing coloration on stainless steel using fiber laser technology. With prior research as a guide, the individual in charge devised a set of parameters, targeting the upper-frequency range, spanning from 50 to 60, coupled with power levels ranging from 10% to 100%. A consistent scanning speed of 750MM/S was maintained, with a minute interval of 0.003 mm, aimed at optimizing heat generation and frequency modulation for coloration purposes.
Utilizing the LightBurn software interface, the individual meticulously delineated the engraving area and initiated the color test. Initial observations revealed a predominantly darkened surface, with faint traces of color emerging under specific viewing angles. Recognizing the need for optimization, the individual contemplated adjustments to scanning speed to enhance color intensity. However, subsequent tests yielded mixed results, prompting further refinement of speed and power settings.
A critical aspect highlighted during the experimentation process was the material’s sensitivity to temperature and composition variations. While initial parameters showed promise on a specific stainless steel substrate, the individual acknowledged the need for adaptability when working with different materials and environmental conditions. This underscored the iterative nature of material testing, emphasizing the importance of refining techniques to suit specific substrates and application requirements.
The material tests provided valuable insights into the intricate dynamics of laser engraving on stainless steel. Despite the inherent challenges and nuances associated with coloration, the experimentation process served as a foundation for further exploration and optimization. By leveraging technology and employing iterative refinement, individuals can unlock the full potential of laser engraving, paving the way for innovative applications and creative expression. Introduction: Laser engraving technology offers versatile possibilities for creating intricate designs on various surfaces, ranging from metals to rocks. This paper delves into two distinct image tests conducted using laser engraving technology: engraving a photorealistic image on a metal dog tag and engraving a fossil image on sedimentary rock. These tests aim to showcase the precision and creative potential of laser engraving in producing detailed and visually captivating designs.
Image Test-
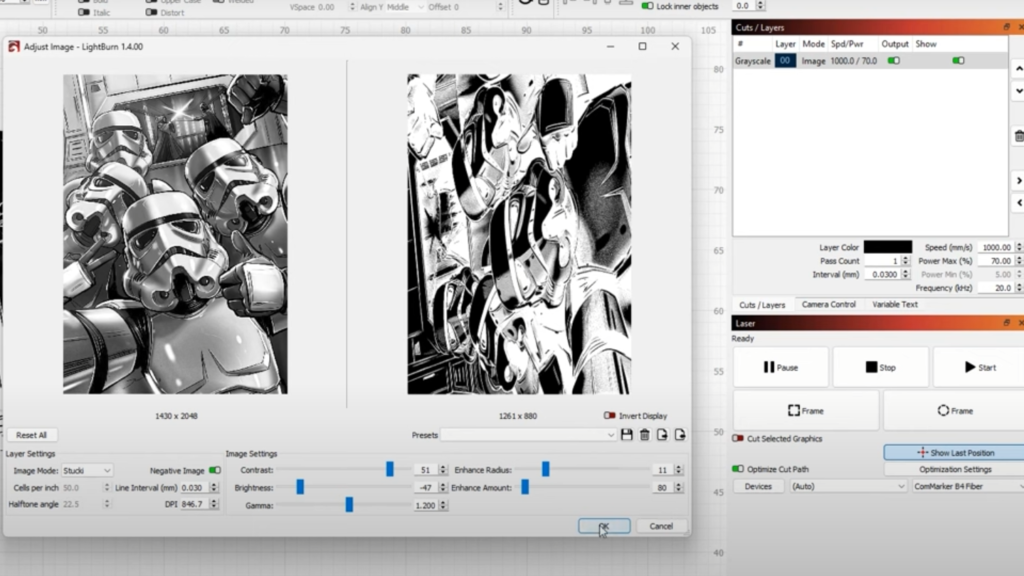
Photorealistic Image Engraving on Metal: The first experiment involved engraving a photorealistic image of a stormtrooper’s selfie onto a metal dog tag. Utilizing Stucky mode and carefully adjusting contrast, enhanced mount, radius, brightness, and gamma settings, the image was optimized for engraving. Despite minor loss of detail in the upper left corner, the outcome was impressive, demonstrating the capability of laser engraving to produce intricate designs on metal substrates with fine point detail.
Fossil Image Engraving on Sedimentary Rock: In the second experiment, a fossil image was engraved onto the sedimentary rock, leveraging LightBurn software for parameter adjustment. Max power, frequency, line interval, and scanning angle were meticulously configured to achieve the desired engraving depth and detail on the porous rock surface. While the results showed a partial engraving effect, variations in surface density and porosity affected the outcome, highlighting the need for further experimentation and parameter optimization.
Plastic Test:
While previous tests have primarily focused on metals and organic materials like wood, this experiment explores the engraving potential of plastic, specifically cast acrylic. The study emphasizes the importance of understanding the composition of plastic materials to ensure safe and effective engraving practices. By utilizing black acrylic blanks, the experiment aims to achieve crisp and clean engravings. Parameters such as speed, power, frequency, and hatch settings are meticulously adjusted in LightBurn software. The results demonstrate the machine’s capability to produce high-contrast and detailed engravings on acrylic substrates, opening up possibilities for applications like keychains and signage.
Brass Test:
In addition to plastic, the study investigates the engraving potential of brass substrates, focusing on challenge coin blanks. Initial tests are conducted using brass sheet samples to determine optimal engraving settings, considering factors such as material thickness and heat absorption. The results provide insights into achieving desired shading and coloration on brass surfaces. Subsequent experiments involve engraving the study’s logo onto brass challenge coin blanks, aiming for high-contrast and well-marked designs. The outcomes reveal the machine’s ability to produce intricate and visually appealing engravings on brass substrates, presenting opportunities for personalized tokens and commemorative items.
Conclusion:
The image tests conducted underscore the versatility and creative potential of laser engraving technology in producing detailed and visually captivating designs on diverse surfaces. From photorealistic images on metal to artistic engravings on sedimentary rock, laser engraving offers opportunities for personalized, promotional, and decorative applications. Further research and experimentation are warranted to refine engraving techniques and optimize parameters for achieving consistent and high-quality results across different materials and surfaces.
Laser engraving technology offers a wide range of possibilities for creating intricate designs on different materials. This paper focuses on testing the engraving capabilities of a laser machine on plastic and brass substrates. The experiments aim to showcase the potential and versatility of laser engraving in producing high-quality and visually appealing marks on diverse materials.
The experiments conducted highlight the versatility and potential of laser engraving technology in creating detailed and visually captivating designs on plastic and brass substrates. From acrylic keychains to brass challenge coins, laser engraving offers opportunities for personalized products and promotional items. Further exploration and experimentation with different materials and engraving techniques are encouraged to unlock the full creative potential of laser engraving technology in various applications.
We sincerely appreciate Vintauri sharing his video with us. https://www.youtube.com/watch?v=-Y8RjmpwZf4&t=175s is the link to the video.